Plastic piping is not only widely used in new installations, but also in repairing existing installations. Even in a metal water piping system, maintenance and repairs can introduce plastic pipe fittings that interrupt the electrical continuity of the system. These fittings can also significantly reduce the length of piping that can act effectively as a grounding electrode. Water utilities do not commonly install jumper wires around the fittings to maintain electrical continuity. In fact, many utilities discourage the connection of buried parts of metal water piping systems to the electrical system. They say that electric current through the pipe can hasten corrosion and affect the taste of the water.
With the introduction of nonconductive plastic water piping systems, the burden of providing a low-impedance connection to earth at the service equipment falls on other types of grounding electrodes. The research project described in this article is being conducted to evaluate buried electrodes to be sure they can handle the job.
Background
A project to evaluate grounding electrodes began a few years ago in Clark County, Nev. (Las Vegas area), when questions arose about the adequacy of certain types of grounding electrodes. Subsequently, the National Fire Protection Research Foundation (NFPRF) got involved, and a Technical Advisory Committee (TAC) was organized to gather information about the performance of grounding electrodes for building wiring systems. Today, the TAC is composed of representatives from NFPRF, NFPA, UL, electric utilities, industry associations, electrical contractors, municipalities, the U.S. Army, instrument manufacturers, grounding rod manufacturers, the entertainment industry, and possibly more, as the list of members grows. The organizations represented on the TAC are sponsoring the long-term research project on grounding electrodes. The project is being managed by the NFPRF.
The purpose of this grounding electrode research project is to develop data to evaluate the corrosive effects of various weather and soil conditions around the United States on different styles of grounding electrodes, and how an electrode’s ability to carry ground current is affected. The project includes long-term testing of grounding electrodes buried in the soil at a number of test sites. Presently, test sites are located near Staunton, Va., and Las Vegas. This spring, the third and fourth test sites are planned for installation in Texas and on UL’s campus in Northbrook, Ill. Other sites are proposed for New York, Montana, and central Florida (on the Disney property). The testing involved will explore grounding resistance and the electrical integrity of the electrodes over time in various types of soil to determine whether moisture content, pH levels and other soil conditions can corrode grounding rods enough to degrade grounding paths to an unacceptable extent.
Expected to take approximately 10 years or longer, the research project consists of monthly measurements of electrode-to-earth resistance; and measurements of soil moisture content, soil pH, temperature, precipitation and other environmental conditions. Some electrodes in the project carry a small current from a dc power supply. At the end of the testing period, the electrodes at each site will be exhumed and weighed to determine weight loss due to corrosion. The data will be sent to NFPRF for compilation and analysis. NFPRF will issue a comprehensive report that will show how the specific grounding electrodes fared at specific site locations. Recipients of the report will then be able to make judgements regarding the adequacy of specific electrodes in certain soils, and whether some grounding electrode systems may warrant further study. Changes in the codes covering grounding methods could result from the data obtained from this project.
Why are Electrical Systems Grounded? Why is Grounding Important?
According to Article 250 of the National Electrical Code® (1996 edition), systems and circuit conductors are grounded to limit voltages on a system with respect to earth and items that are in contact with the earth. The voltages can be caused by lightning, line surges or unintentional contact with higher voltage lines. Grounding the system also stabilizes the voltage on the system with respect to ground during normal operation. A low-impedance connection at the service equipment between the grounded conductor of the electrical system and earth can enhance the longevity of the electrical insulation and reduce the risk of electric shock. Concerns regarding electric shock include not only the effects of faults in electrical insulation, but also the voltage that can appear between “grounded” accessible parts under normal conditions. These voltages are usually low, but can be undesirable in areas where people have simultaneous access to the earth and to equipment grounding conductors that are, in turn, connected at the service equipment to the grounded circuit conductor of the system.
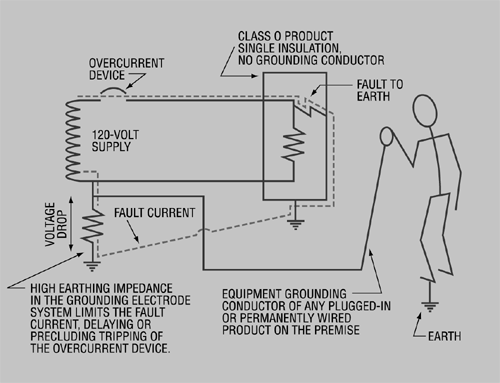
An example of an electric shock scenario created in part from a poor grounding connection to earth is shown in Figure 1. In the figure, an electrical product is in contact with the earth through a conductive part of the building structure, perhaps involving its mounting means. A low-impedance fault occurs between a live part inside the product to its enclosure. Fault current flows as indicated by the dashed line in the figure, but the impedance of the grounding electrode system limits the magnitude of the fault current. The opening of the overcurrent device is delayed, or the overcurrent device carries insufficient current to operate.
A person in contact with the earth and any conductive part connected to a grounding conductor of equipment plugged in or permanently wired anywhere in the building while the fault current flows could experience an electric shock, if the voltage dropped across the grounding electrode system is high enough. This situation is aggravated when the person is more susceptible to the effects of voltage across the body (for example, when the person is in a swimming pool or spa).
An overcurrent device, such as a circuit breaker, requires a minimum of 110 percent of its rated current to trip and open a circuit. For a 120-volt, 20-ampere circuit, for example, the total impedance of the loop carrying the fault current, according to Ohm’s Law, must not exceed 5.5 Ohms (i.e., 120V/22A). The grounding electrode contributes in part to this total value, and therefore, the resistance to earth of the grounding electrode system alone might have to be significantly lower than 5.5 Ohms.
What are Some Typical Grounding Electrode Designs
Article 250 of the National Electrical Code covers grounding. Grounding electrodes are described in Sections 250-81 and 250-83. Typical grounding electrode designs include rod and pipe electrodes, grounding plates, chemically charged electrodes, and concrete-encased electrodes.
What is The Scope of the Project and What Types of Electrodes Will be Installed at the Test Sites
The scope of the research project includes many types of grounding electrodes permitted by the NEC According to the scope, the project does not include water piping systems and building steel, nor does it include the grounding conductors and various equipment used to provide grounding paths elsewhere in a premise’s wiring system. Since the project focuses on building systems, it does not necessarily cover all types of electrodes used by electric utilities.
The Northbrook, ILL., Site—Installation and Testing
The Northbrook, Ill., test site is similar to other test sites in the NFPRF study. A 100′ by 200′ test site will be located on the east side of the UL property. Within the test site, a total of 63 grounding electrodes will be buried. There will be two fields Ñ one passive (no electrical current applied), and one much smaller, active field (electrical current of approximately 5mA dc applied). The electrodes, installed horizontally or vertically in the site, will represent designs permitted by the NEC® in a number of configurations.
Fifty-seven electrodes will be buried in the passive field. Some of these electrodes are specifically designed and manufactured as grounding electrodes, while others are simply various types of pipes and rods permitted by the NEC® for grounding use. Electrodes include solid reinforcing bars, metal rods, galvanized steel pipes, copper conductors, concrete-encased electrodes, plates and chemical electrodes. In the passive field, 30 electrodes will be vertically driven or buried in augered holes up to 1-1/2 feet in diameter and 10-feet deep. The remaining 27 electrodes will be buried in horizontal trenches 4-feet deep.
The chemical electrodes for installation in the passive field are hollow copper tubes with small predrilled weep holes along their lengths. The tubes are filled with salts. When the salts come in contact with moisture, an electrolytic solution is formed, promoting good electrical contact with the earth. Some of these chemical electrodes will be encased in bentonite, a material that also promotes good electrical contact with the earth.
In the active field, a current of approximately 5mA dc will flow through vertical electrodes of two types — 5/8″ copper-clad steel rods, and 3/4″ trade-size galvanized pipe. The current represents the dc component of the electrical ground current in a hypothetical scenario.
Direct current flows through the grounding paths of building wiring systems when products are used that rectify the load current. Electrode deterioration/corrosion is caused by electrolysis from direct current flowing through grounding electrodes. Load currents flow through grounding paths between the service equipment and the utility transformer because the grounded circuit conductor is connected to earth at more than one point. The NEC® requires one of these grounding points to be connected at the service equipment of a building to limit the voltages on the system with respect to earth. Utilities ground systems along entire power distribution networks for the same reason.
The importance of the active site is to illustrate how direct current can accelerate the corrosion of grounding electrodes, in contrast to the electrodes in the passive fields that do not have dc current flowing through them. The active site will also show the distribution of the corrosion along the length of the electrode. If, for example, the corrosion is concentrated near the point of connection to the grounding electrode conductor, early failure of the grounding electrode may result with minimal loss of material, leaving most of the electrode in the soil, but disconnected from the electrical system.
What Measurements Will be Used to Evaluate an Electrode in the Test Site?
All electrodes will be weighed prior to burial and again at the end of the project after they’ve been exhumed and cleaned. This process will determine the amount of electrode material lost to the earth by way of electrolysis and corrosion. Weight retention is an important factor indicating the ability of an electrode to provide a sound, low-impedance connection to earth over time.
In addition, the electrode-to-ground resistance will be periodically measured during the course of the project. The probes for the instrumentation and each electrode in the project will have buried leads terminating in a junction box where resistance measurements can be taken. Records of variable environmental conditions will be collected. Figure 2 illustrates the resistance measurement method.
How Are Grounding Electrodes Installed at the Northbrook Site?
The installation equipment includes a backhoe and a power auger. The backhoe is used to dig 12 trenches approximately 80-feet long for horizontal burial of 27 electrodes. Smaller trenches will accommodate instrumentation leads. The power auger is used to drill holes for vertically positioned electrodes, except that driven ground rods are installed by forcing them into the ground without the use of an excavated hole. Following site excavation, the electrodes are placed in the trenches and holes. A copper lead is connected to each electrode, and terminates in a junction box where the resistance measurements from electrode-to-earth will be taken during the term of the study. Prior to backfilling, the leads will be placed in plastic flexible conduit that serves as mechanical protection when the trenches and holes are filled with earth. The conduit also permits easier replacement of damaged leads during the course of testing, if necessary.
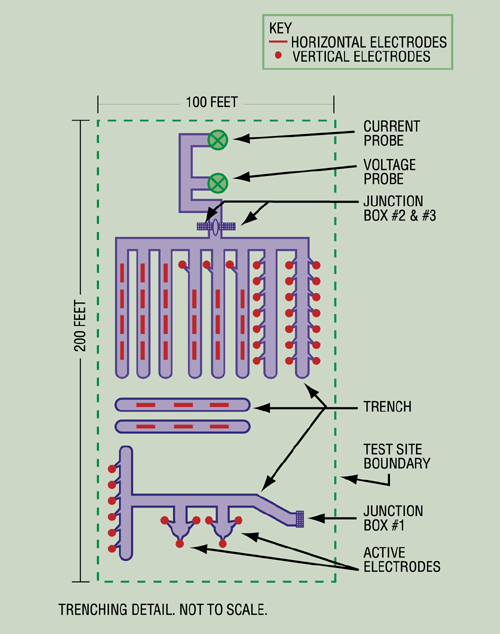
Figure 3 illustrates the trenching detail.
Summary
The results of this study will provide valuable information for builders, designers, utilities, code authorities and others who build, install, inspect or maintain electrical systems. Future construction is likely to introduce more plastic water pipe, and thus, new designs of grounding electrodes for electrical systems may be required. These new designs for grounding electrodes — a simple concept — must respond to the complicated challenges of corrosion, electrolysis and accelerated deterioration that have become important problems to solve in our increasingly complicated environment.
For more information on this project, call Peter Boden at UL in Northbrook, Ill., at (847) 272-8800, ext. 42011; or e-mail him at bodenp@ul.com. Call Walter Skuggevig at UL in Melville, N.Y., at (516) 271-6200, ext. 22312; or e-mail skuggevigw@ul.com. Or write Doug Brown at the National Fire Protection Research Foundation, 1 Batterymarch Park, Quincy, MA 02269; call (617) 984-7281; or e-mail dbrown@nfpa.org.
Note: [1] K. Michaels. “Earth Ground Resistance Testing for Low-Voltage Power Systems,” IEEE Trans. on Industrial Applications, pp. 206Ð212, Vol. 31, No. 1, Jan./Feb. 1995.
This article was reprinted by permission of On the Mark.
Copyright © 1998 by On the Mark. Reprinted with permission.
Find Us on Socials