In this article, we will review inspection items we need to understand related to two installations we don’t usually look at every day. Signs and pools, in my experience, have been tossed around between electrical inspectors and combination inspectors. For years, pools were assigned by default to electrical inspectors due to the critical safety issues created by the mix of water and electricity. If not done properly, the possibility of a dangerous situation is all too likely. The other side of this is that, depending on soil conditions and the type of pool construction, the structural design is also very critical. This situation also means that a good structural inspection is required, which is often done by a building inspector.
When we discuss signs and sign inspections, we also have several important factors to consider. Some entities decide that signs do not need inspections; others think they only require an electrical inspection, and still other departments look at the structural and electrical portions of an installation. Some jurisdictions don’t pay a lot of attention to signs since they don’t have any occupancy, so they don’t appear to have a lot of liability from a construction and inspection perspective. However, in Las Vegas a 362-foot tall sign experienced a structural failure duriang a high wind event, and portions of it came crashing down. Electrically, some of the newer signs are requiring electrical services up to 2000 amps to drive the sophisticated reader boards and television style signage, along with the air-conditioning units required for these signs to keep them operating. The newer electronic signs may draw less power, but they all require some type of voltage converter/power supply which produces heat and, therefore, needs adequate cooling to survive, especially in areas like the southwest desert where I live.
Additionally, some signs may generate voltages with potentials between 7500 and 15,000 volts, creating an additional level of needed protection. As you can see, signs must have proper inspections to insure safety for the public and those who need to service and maintain them.
Let’s get started on the basics of sign inspections based on Article 600. Please review 600.2 for definitions related to signs. Unless you are in the sign business, you may not realize the difference between a neon sign and a skeleton tubing sign. Also, in the 2011 version of the NEC, they have added a new definition for LED Sign Illumination System to help us to keep up with new technology related to illumination.
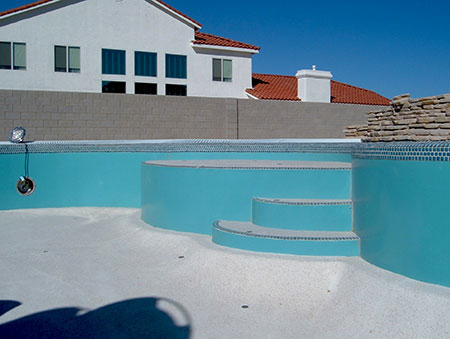
The first code requirement I want to point out is the need for Listing. This requirement is covered in 600.3, which clearly states that a sign shall be listed and installed according to the listing instructions unless approved by special permission. In my jurisdiction, we made this simple by requiring all signs be listed, relieving the jurisdiction of liability.
The next requirement is 600.4 Markings, which informs us what information is required to be marked on signs to assist us in performing our inspections. Information such as manufacturer’s name, voltage and current rating is required. In 600.3(C) and (D), a new requirement has been added that covers the visibility of the marking and listing labels. Previously these had to be on the outside where they were visible, which made it simpler for inspection. However, complaints came in that the labels were distracting and causing aesthetic issues for those signs that are considered “works of art.” Now these labels are not required to be visible after installation and only need to be located where they can be seen during servicing. Naturally, these labels have to be durable and permanent and suitable for the environment, such as weatherproof when exposed in a wet location.
This new allowance does create an inspection headache, because if these markings are in a location where an inspector cannot easily see them, then he or she will need a way to verify that they are there. I don’t know any inspection department that has equipment that allows them to get up to a sign and open it to verify these labels. In my former jurisdiction, we would have to coordinate these inspections with the sign companies so that they could provide access to the signs for inspection. Every morning sign companies would call to see what time they could expect the inspector to get to their job.
The next code item is 600.5 Branch Circuits, and (A) deals with the required branch circuit. This requirement is something that needs to be caught in plans check and during the construction or tenant improvement of the facility. The code states that each commercial building and occupancy accessible to pedestrians shall be provided with a least one outlet in an accessible location at each entrance to each tenant space for a sign or outline lighting system. It goes further to say it shall be a 20 ampere circuit that serves no other load. This requirement is often missed and tossed back and forth between the shell contractor and the tenant improvement contractor. The code doesn’t say who is responsible; it just states we shall have one. Put this on your checklist for commercial buildings.
In 600.6 we find the disconnect requirements for signs: it shall disconnect the ungrounded conductors, and if it is fed by more than one ungrounded conductor, then it needs to disconnect each such conductor simultaneously. The location shall be within sight of the sign it controls. If it is located where it might not be in sight of all the portions of the sign it controls, then it must have a lock-out feature in accordance with 110.25.
Grounding of signs is another inspection item we need to be very diligent about. Grounding and Bonding is addressed in 600.7, and this is one part of the NEC that is very well coordinated with Article 250 Grounding and Bonding. Almost every paragraph of 600.7 references a requirement in Article 250. Some of the key items are the requirement for all signs to be grounded, and that they shall have an equipment grounding conductor based on the size of the circuit protective device feeding the sign.
The bonding of signs has some special requirements that inspectors have to insure get done properly. First, metal parts and equipment of signs shall be bonded together to the transformer or power supply equipment grounding conductor; this means the metal enclosures that house the components, or any metal back piece that is used to support signage. There is an exception related to the newer use of LED lighting that uses Class 2 power supplies to provide the low voltage for the LED circuits. If a Class 2 power supply is used, then we don’t need to bond the remote metal parts of a sign to the equipment grounding conductor.
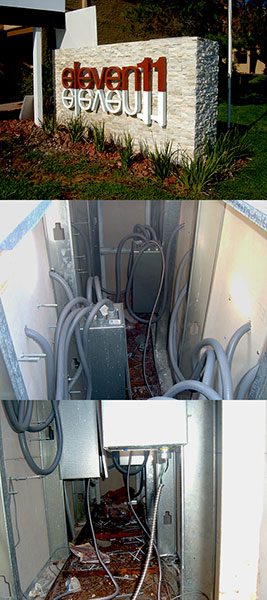
The last item that comes to mind regarding sign and inspections is covered in 600.21(D) and (E). This is Working Space and Attic and Soffit Locations. First, for the working space requirement, you should have a clearance which represents a 3 foot cube to work on any ballast, transformer or power supply. When these are located in attics or building soffits then we must have an access door at least 36 inches by 22.5 inches. Why the odd number of 22.5? This allows for 24 inches on center framing of wood members. Once you have the access, you have to have a passage-way at least 3 foot high and 2 foot wide to get to the 3 foot cube area. This passage-way shall have a permanent walkway at least 12 inches wide from the point of entry to each piece of equipment. The last item is that you must have a light near the equipment so you can see to service it and the switch for this light shall be at the usual point of entry to access the equipment.
Please review the rest of Article 600 related to other sign requirements. Due to space limitations, I’ve covered just the basics of inspections for signs.
Now let’s move to Article 680 Swimming Pools, Fountains, and Similar Installations. As I often do, I will cover what I consider the highlights of this article. I challenge each of you to read the definitions on your own since there is over a full page of these that you have to be familiar with to understand the unique conditions related to pools.
As we all know, electricity and water don’t mix too well, so you will find special grounding requirements within Article 680 to minimize the risks. The first rule to point out for enforcement is 680.6 Grounding, which gives us the ground rules for what is required to be grounded and how to do it. A reference is given to Article 250 Parts V, VI, and VII for the methods of grounding, and another reference to Chapter 3 for the allowable wiring methods, followed by a laundry list of items to ground.
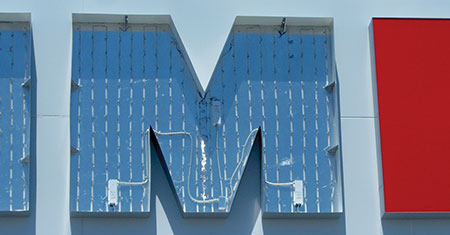
Article 680.8 Overhead Conductor Clearances is one of the toughest enforcement issues we have, as this is a clearance requirement for items that are not under the control of the property owner or the contractor(s) doing the pool installation. This is the clearance required to the utility, phone and other wiring that may be passing above on easements. The first item we need to define is the level at which we start our measurement. It states that the measurement is from the maximum water level. If you read the definitions as I mentioned above, you will know this is the level that water may reach when it finally spills over the pool walls. These requirements are covered in Table 680.8, and as you can see from the table, we have clearance requirements from the water, diving, and observation stands.
The basic requirement is that a clearance from insulated cables operating up to 750 volts must be at least 22.5 feet. This clearance seems like a great distance; however, the thing you have to keep in mind is how we service pools. We use aluminum poles that are extendable to somewhere around 14 or 15 feet, which in the hands of a 6-foot tall person could easily reach about 20 feet into the air. We are trying to insure these overhead conductors are far enough away that accidental contact cannot be made. Communications Systems as outlined in 680.8(B) only require a 10 foot clearance, but our issue is that most of these systems are not easily identified and distinguished from Network-Powered Broadband Communications systems that are enforced as per Table 690.8.
These clearance issues will sometimes delay the construction of a pool until the utility can perhaps change the way an overhead drop is made. A utility can at times do what is called a mid-span tap that will allow these drops not to pass near a pool. We found that the pool contractors got pretty good at recognizing these issues before we were asked to do our first inspection, since they had a difficult time getting payment when the customer couldn’t swim due to a code violation and an incomplete pool.
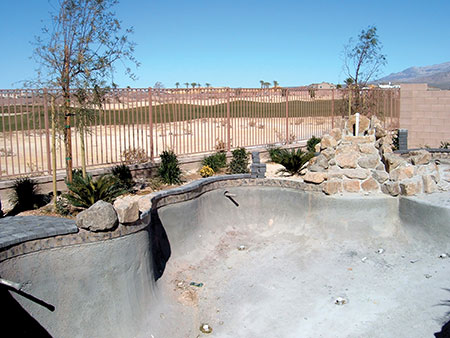
Motor details related to pools are covered in 680.21. Described here are the different wiring methods and locations, but the one item that is fairly new is GFCI protection. All motors that are 120 through 240 volts with branch circuits rated 15 or 20 amperes is required to have GFCI protection; this is a new requirement since the 2008 code.
The requirements for Lighting, Receptacles and Equipment around pools are covered in 680.22. Points of interest here are the requirement for any receptacle to be at least 6 feet from the inside walls of a pool, and we must have at least one receptacle located within 20 feet of the pool. This receptacle is needed for anyone trying to work or service this pool. Also, any and all receptacles within 20 feet of the inside walls of the pool are required to be GFCI protected. The rest of 680.22 deals with the location and requirements for luminaires (lights) around a pool, new lights and how to deal with existing lights, clearances required and GFCI protection.
Underwater Luminaires in 680.23 covers the requirements for proper installation. Basically, these lights are divided into two categories, low voltage, supplied by a transformer or power supply, and line voltage. If they are line voltage (120 volts) then they require GFCI protection as outlined in 680.23(A)(3). The most common fixtures seen are wet niche forming shells, meaning the pool water is within the niche and surround the light housing. These may be metallic (brass or stainless steel) or made of PVC. The wiring to these forming shells may be in metal raceways approved for the environment to deal with any corrosion issues that may exist. At times you may see red brass conduit used. The other option is to run non-metallic conduit to the forming shell, which is generally PVC. If PVC conduit is selected, then you must have an 8 AWG bonding jumper installed within the conduit and it must terminate in the forming shell and have an encapsulating compound installed over the termination to protect this termination from the corrosive conditions that may exist within the pool water. Also, please note that the forming shells have a grounding lug on the outside which must have a bonding jumper installed and connected to the rebar that makes up the conductive pool shell; for example, if it is a concrete reinforced pool.
The line side of the conduit feeding to the forming shell must originate in a Junction Box of Electrical Enclosure that meets the requirements of 680.24. In (A)(1) of this section you will find the construction requirements for this junction box; if using an enclosure, it must meet the requirements of (B)(1). There are some special requirements for these: one is the requirement for a hub, either threaded for conduit using threads or a non-metallic hub for PVC conduit. You can review the other items, but generally if the installer buys a listed pool light junction box and installs it per the installation instructions, it will typically meet the code requirements of this section.
The junction boxes must be located at least 4 inches above ground level and at least 8 inches above the maximum water level, and lastly, at least 4 feet from the inside wall of the pool. Check this carefully, as pool lights cost more the longer the cord, so they may try to place this junction box as close as possible to the light niche.
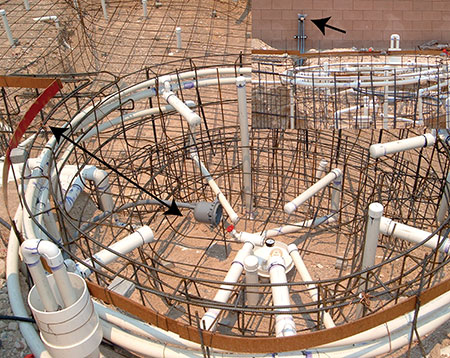
One special inspection item to note is 680.23(F)(3), and you must verify this during the inspections. This is the requirement that GFCI-protected conductors shall not occupy the same raceway, box or enclosure as other conductors. There are four exceptions to this requirement to review. Let me explain why this is so important: a GFCI-protected circuit is there for the protection of personnel. If we mix conductors, GFCI and non-GFCI protected, and something happens in that conduit that causes a short circuit, we may create an energized, unprotected circuit that could cause physical harm to a person.
The last article we will cover related to pools is 680.26 Equipotential Bonding. The purpose of this requirement is outlined in 680.26(A), which states it shall be installed to reduce voltage gradients in the pool area. The voltage gradients may come from electrical devices related to the pool or other electrical equipment nearby. At times, the hazard may come from a utility that has a loose or failed connection nearby. I have personally experienced enough voltage in the water of a pool that it would make my solenoid voltage tester read 110 volts when one probe was stuck in the earth, and the other dropped into the water. The cause was a failed connection on a utility pole on the opposite side of the pool.
To minimize issues, we want to create a common potential between all the items listed in 680.26(B)(1) through (7). The first item listed is the conductive pool shell. In concrete reinforced construction, the structural steel of the pools makes a huge oversized Ufer ground, thus possibly putting everything nearby at a different potential if we don’t also bond these items. Some of the items on the list to bond to the pool shell is the perimeter surface (which is the walking surface around the pool), see the list in 680.28(B)(2) for details on how to accomplish this. Other items to bond are any metal components related to the pool, underwater light forming shells, metal fittings such as pool handrails, ladders, diving board, and slide. All these items have lugs for an 8 solid copper bonding conductor connected to the rebar. Other items to bond include any electrical equipment related to the pool water circulating system, such as pumps, heaters, and blowers.
The last item to bond is the most difficult to accomplish, and that is any fixed metal parts within 5 feet of the outside wall of a pool. This is a laundry list of items such as raceways, metal piping, metal awnings, metal fences and metal window and door frames. The challenge with this requirement is that the bonding jumpers usually are run from the rebar cage of the pool structure for each of these; and if they miss one, and the concrete deck has been poured, it makes it more difficult to accomplish. Window frames seem to be the biggest issue, and these connections are not too aesthetically pleasing to the eye at times.
Remember that the purpose of this requirement is to place anything that may conduct electricity at the same potential as the water within the pool. We’ve all heard the stories and news reports about people being electrocuted in or around pools and the requirements outlined within Article 680 are there to prevent these situations from happening. The challenge at times comes after we have done our inspections, as we rely on qualified service people who may work on these facilities to also know the code and to comply with the NEC. I know I may be dreaming here, but there is always hope.
Thanks for reading, and don’t forget to get out your NEC and read these two articles.
Find Us on Socials