Electric utilities face the challenge of managing aging and unsupported legacy automation and monitoring equipment at their substations and pole-tops. This equipment is critical for accessing data from intelligent electronic devices (IEDs) for measurement and protection, automating key functions, and enabling remote users to securely control power-system devices.
Increasingly, outdated legacy technology such as remote terminal units (RTUs) needs to be updated to keep up with evolving performance requirements, communication needs, and increased security compliance protocols. The need can also be driven by concerns over vendor support or when there is a major deficiency a vendor is not addressing with the equipment.
When this occurs, utilities often take the opportunity to pilot and deploy new substation automation platforms as part of the upgrade. Given recent advances in automation, new all-in-one solutions:
- effectively reduce the number of hardware components in each substation improve integration with existing IEDs and RTUs;
- simplify data access and configuration through integrated, web-based HMI, SCADA and alarm annunciator interfaces; and
- facilitate cybersecurity compliance to meet NERC CIP requirements.
A window of opportunity for SRP
Today, the Salt River Project (SRP) is in the process of updating its substation automation platforms. The energy company manages a large field operation of over 300 substations across a 2900 square mile service area in central Arizona in support of over one million customers.
For SRP, the process of exploring upgrade options began more than two years ago when the vendor that supplied its RTUs discontinued support for the product.
“We have been using the primary RTUs in our system since the mid-nineties, and they were simply outdated,” said Josh Manski PE, senior engineer at SRP. “Although we began the project because our vendor discontinued support for the RTU, we really saw it as an opportunity to integrate the next generation of substation automation systems to assist our security compliance efforts and provide greater interoperability with other parts of the system.”
After sending out a Request for Information/Proposal (RFP) to the nation’s top vendors of RTUs and also communication and automation processors, SRP scheduled demos and conducted a full lab evaluation of all the products involved.
SRP ultimately selected Pennsylvania-based NovaTech, as their substation automation provider. The company has worked with customers in the electric power transmission and distribution substation market for more than 30 years.
The company’s Orion Substation Automation Platform is a communication and automation processor that can connect to nearly any substation device in its native protocol, perform advanced math and logic, and securely present the source or calculated data to any number of clients in their own protocol.
The Orion can be integrated with any equipment, including competitors, and is often connected to microprocessor-based relays, meters, event recorders, IEDs, and RTUs. It is then connected to an existing enterprise network or SCADA system.
According to Manski, NovaTech was selected, in part, based on its willingness to configure features of the Orion platform to meet SRP’s specific requirements.
“Our engineering team tried to be really forward-thinking as we were implementing these upgrades,” explains Manski. “We kept asking ourselves how we could configure the product so it would make our life a lot easier going forward.”
For SRP, this included ensuring field engineers or technical staff could modify the master configuration files to tailor the system to each site.
At SRP’s distribution sites, there is greater consistency, and the Orion platform easily supported existing standards and configurations used for decades. However, there was more variability in terms of configuration at each transmission substation, and so a templated approach did not work as well.
Using Orion, Manski and his team were able to build a master configuration file that encompassed SRP’s base standards but still allowed the field engineer to modify or delete aspects that did not apply to a given site.
This also simplified training, an important feature given SRP rotates new engineers through a variety of roles every six months as part of a two-year onboarding program. The training includes learning all the equipment, including the Orion, and how to program it.
“Our new and experienced engineers were very impressed by the ease of configuration and intuitiveness of the Orion platform – so much they stated they preferred working on it over the legacy equipment,” says Manski.
The system also uses open-source web technologies and pre-configured template pages to simplify the building of interactive SCADA and local HMI screens to view data from connected IEDs and RTUs using standard web browsers.
Beyond interface design improvements, the integration of key features such as an alarm annunciator application is one of the areas that substation automation platforms have advanced significantly.
The alarm annunciator in the NovaTech platform is managed through the same WEBserver software. It includes pre-configured pages for data archiving/sequence of events recording, alarm annunciation, one-line diagrams, IED faceplates, control screens, alarms, trending, and communications diagnostics.
For example, any data point in the Orion database, either obtained from attached IEDs or calculated, can be designated as an alarm point and displayed on the tile annunciator.
This can save substantial time when upgrading sites with thousands of alarms.
“It used to take hours for us when we were upgrading a transmission site that had almost a thousand alarms,” says Manski.
Now two years removed from a successful pilot implementation, SRP this year is upgrading 6 transmission substations and 9 distribution sites, with additional generation and distribution feeder automation planned. The utility anticipates it will ultimately replace more than 300 RTUs and install 500-600 Orion systems.
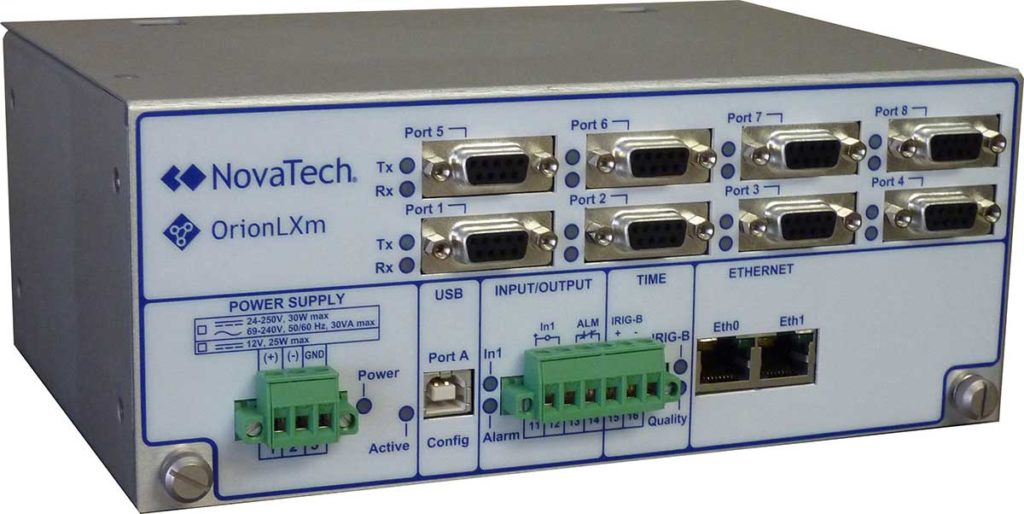
Automation Upgrade at Hoosier Energy
In the Midwest, Bloomington Indiana-based Hoosier Energy also had to review its substation automation technologies. The electric cooperative, founded in 1949, provides wholesale power and services to 18 members through a nearly 1700-mile transmission network.
“Our RTU vendor went out of business,” explains Lance Simpson, a Hoosier Energy communication engineer. “We needed a vendor that would be a reliable source of maintenance and spare parts.”
The energy company used an extensive RFP process before selecting NovaTech.
“A large driver for our choice of system was the user interface and how comfortable our technicians felt with it,” says Simpson. “It needed to be user-friendly not only from an engineering design perspective but also from the technicians’ perspective. The ease of building master configuration files using the NovaTech Communications Director [NCD] makes their work easier.”
Hoosier Energy technicians often use the terminal interface to view traffic on the various communications ports. They also move files and save multiple configurations on the same box for the HMI. “With everything organized through the same interface, there is less training to do because the learning curve is not nearly as steep,” says Simpson.
The utility finds the simplicity of the interface particularly useful for testing when it will need to pull alarm logs off to view them and trend values over time.
The consolidation of features in a single unit has also saved Hoosier Energy space and money. According to Simpson, “having an integrated tile annunciator tool has allowed us to install annunciator displays in stations where costs or space previously prohibited us from doing so.”
While the utility primarily sources off-the-shelf RTUs and parts such as terminal blocks, field wiring, and power supplies from NovaTech, it also sources integrated distribution enclosures. These are complete cabinets or enclosures designed for distribution SCADA applications in outdoor environments. Due to the challenging environmental conditions, these are larger in scope and require a separate battery charging system and environmental controls.
The combined efficiencies that Hoosier Energy has discovered using integrated technologies have had a significant overall impact. “Based on all the things the Orion platform can do, we have certainly seen cost savings and just an overall improvement in ease-of-use,” said Simpson.
Since 2012, Hoosier Energy has deployed 10 new large RTUs at its transmission stations and 20 more smaller applications at the distribution level. According to Simpson, the energy company will continue to replace and upgrade its technology at the rate of 2-5 transmission substations each year.
For more information on substation automation platforms, visit the NovaTech website at www.novatechweb.com or call (844)-668-2832.
Find Us on Socials