Most, if not all of us, have some type of familiarity with the Occupational Health and Safety Administration (OSHA). But how familiar are you with the background of OSHA? Why was it established? What are the regulations associated with the electrical industry? Are they involved with NFPA 70E, Electrical Safety in the Workplace? Continue reading for the answers to these and other construction industry-related safety questions.
Occupational Safety and Health Act Overview
OSHA is part of the Department of Labor (DOL). The act establishing the DOL was signed on March 4, 1913, by President William Howard Taft, the direct result of a multi-decade effort by organized labor for a voice concerning safer and more desirable working conditions. The DOL’s purpose is “to foster, promote, and develop the welfare of the wage earners, job seekers, and retirees of the United States; improve working conditions; advance opportunities for profitable employment; and assure work-related benefits and rights.”
Fifty-seven years after the DOL was established, the Williams-Steiger Occupational Safety and Health Act was signed into law on December 29, 1970, by President Richard M. Nixon. This followed the very vigorous debate that had begun during President Lyndon B. Johnson’s term. The debate among government, business, and organized labor concerning the extent to which federal authority would create and enforce workplace safety and health standards lasted many months before being successfully voted on. The Act is named after its author, William Steiger, who served the state of Wisconsin’s sixth district in the U.S. House of Representatives from 1967 to 1978.
OSHA requires that every employer covered under the Act furnish employees a place of employment which is free from recognized hazards that are causing or are likely to cause death or serious physical harm to employees. It also requires that employers comply with occupational safety and health standards. Additionally, employees must comply with standards, rules, regulations, and orders issued under the Act that apply to their own actions and conduct. It includes an authorization for the DOL to conduct inspections and to issue citations and propose penalties for alleged violations. The inspection process includes questioning employers and employees in connection with research and other related activities. Although signed into law by President Nixon in December of 1970, the Act became effective on April 28, 1971, the official “birthday” of OSHA. On May 29, 1971, OSHA published its initial standards package in the Federal Register, the official journal of the federal government. The initial standards package contained existing federal standards and national consensus standards for general industry, construction, and maritime, just to name a few industries.
George Guenther, leader of the DOL’s Bureau of Labor Standards, was the first person named as Assistant Secretary of Labor for OSHA. Under his initial guidance, the main focus in 1971 was to recruit and train effective compliance officers. Also established was a field structure of 10 regional offices, 49 area offices, and 2 maritime offices, all scattered throughout the country in major cities. Efforts then began to educate employers concerning compliance requirements. This included education recognition programs to promote safe and healthy workplace practices. On January 17, 1972, the OSHA Training Institute (OTI) was established to train compliance officers and industry stakeholders on safety in the workplace. The first home of the OTI was in a small building near the end of a runway at O’Hare Airport in Chicago. The first five industries targeted for safety hazards were marine cargo handling, roofing and sheet metal work, meat and meat products, mobile home transport equipment, and lumber and wood products. Five health hazards were also put in the crosshairs: asbestos, lead, silica, carbon monoxide, and cotton dust.
In December of 1975, Morton Corn, professor of occupational health and chemical engineering at the University of Pittsburgh, was sworn in as the new Assistant Secretary of OSHA. He focused on regulatory reform and working with stakeholders from all industries to involve them in the entire standards process. His reasoning for this was that final standards and regulations would be better received, accepted, and complied with if they were established with input from a broad base of industry representatives. With that concept in mind, let’s stop at this point with our review of the origin of OSHA and turn to electrical safety as it relates to OSHA. Assistant Secretary Corns’ desire to have a broad base of industry stakeholders involved in standards and regulations promulgation is the same successful strategy NFPA utilizes for standards development and participation on technical committees and code-making panels.
Development of NFPA 70E
In the mid-1970s, OSHA was struggling to develop regulations associated with electrical safety using the National Electrical Code (NEC) as a basis. This was due to the fact that the NEC was, and still is, an installation standard intended to be used by those who design, install, and inspect electrical installations. The NEC is not designed as a workplace safety document. Additionally, OSHA is not a standards development organization with the ability to modify a standard with a process that includes public input, public comments, and public hearings. The result of these roadblocks was an offer of assistance to OSHA from NFPA to develop a standard to address electrical safety in the workplace.
In May of 1975, this offer of assistance was submitted to the Assistant Secretary of Labor for OSHA, who responded that “the subject matter standard appears to have great merit…an apparent need exits for this proposed consensus document.” After receiving this positive feedback from OSHA, the NFPA Electrical Section, NEC Correlating Committee, and NFPA Standards Council moved forward with establishing a committee to develop a document for evaluating electrical safety in the workplace. That document became NFPA 70E, Standard for Electrical Safety in the Workplace. The first edition of NFPA 70E was published in 1979 and like most other NFPA standards, it’s been updated every three years since being published.
OSHA and NFPA 70E Safety Requirements
Now that we’ve reviewed some history concerning OSHA and NFPA 70E, let’s examine specific requirements that affect our industry daily. I think most of us would agree that being on any construction project, at any stage of the job, is dangerous. Add energized electrical equipment to the construction, and safety is compounded greatly. Not to mention the hazards created by trenching, heavy equipment, ladders, scaffolding, welding, overhead work, and cranes, just to name a few. In a perfect world, all these hazards would be able to be eliminated so workers could work each and every day safely. Unfortunately, there is no such thing as the “perfect job site.” We must do the very best we can to avoid or mitigate hazards when necessary and eliminate hazards when possible.
From a strict electrical perspective, the greatest hazard we can expose ourselves to is energized electrical equipment. But the reality is that all of us who have worked in the trade have worked on energized equipment when there really was no legitimate reason not to de-energize it. As with most safety-related instances, we usually are our own worst enemies due to things such as laziness, time constraints, bad habits, or simply not being aware of the risk. Annex K in NFPA 70E provides interesting and compelling information concerning hazards associated with energized equipment such as an arc blast (see Table 1).
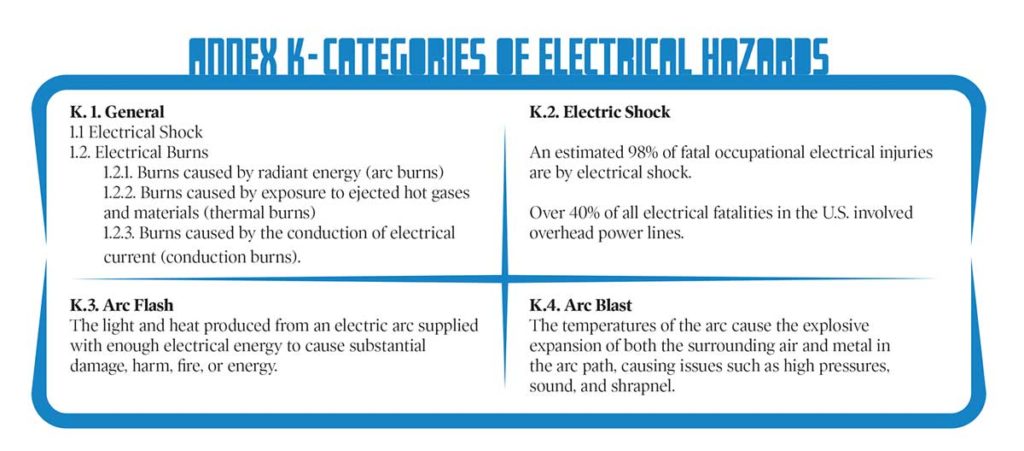
The temperatures of the arc cause the explosive expansion of both the surrounding air and the metal in the arc path. In an arc blast, copper will expand by a factor of 67,000 times when it turns from a solid to a vapor. Molten metal can be expelled away from the arc at over 700 mph. At this speed, the metal is moving fast enough to penetrate the human body completely. The extremely high pressures associated with an arc blast can knock workers off ladders, rupture eardrums, and collapse lungs. If that information is not enough to get electrical worker’s attention to the life-threatening hazards associated with energized work and an arc blast, then they may want to rethink their career choice.
Energized Work and Electrical Safe Work Conditions
Let’s review the three allowances for justification of energized work according to OSHA 1910.333(a)(1), which is mirrored in NFPA 70E Section 130.2(A), Energized Work.
- Energized work is justified if de-energizing equipment introduces additional or increased hazards. Examples of this are the interruption of life support equipment, shutting down of a hazardous location ventilation system, or the deactivation of emergency alarm systems. All of these would pose a greater hazard if de-energized, which OSHA and NFPA 70 recognize.
- De-energizing is infeasible due to equipment design or operational limitations. One example is performing diagnostics and testing of electric circuits such as air conditioning systems and industrial machinery, which most likely require the equipment to be energized in order to troubleshoot performance issues. Another example is equipment that is part of a continuous process, such as conveyors.
- De-energizing equipment operating at less than 50 volts is not required where there will be no increased exposure to electrical burns or to an explosion due to electric arcs.
In ALL other instances, OSHA and NFPA 70E require equipment to be de-energized and put into an electrically safe work condition. Concerns about things like inconvenience, cost, scheduling, and hardship are not part of the equation when associated with the justification for energized work.
I mentioned the term electrically safe work condition, which is defined in NFPA 70E and established when all the requirements of Section 120.5, Process for Establishing and Verifying an Electrically Safe Work Condition, are satisfied.
“Electrically Safe Work Condition. An electrical conductor or circuit part has been disconnected from energized parts, locked/tagged in accordance with established standards, tested to ensure the absence of voltage, and grounded if determined necessary.”
This includes verifying all sources of electric supply to equipment, properly interrupting the load current before opening the disconnect device for each source, visually verifying (if possible) that all blades of the disconnect device are open or that draw-out type breakers are fully withdrawn, releasing any stored electrical energy, releasing or blocking any stored mechanical energy, applying lockout/tagout devices, using adequately rated test instruments to test each phase conductor or circuit part using the live-dead-live method, and finally, if induced voltages are possible or stored electrical energy exist, grounding the phase conductors or circuits parts before contact.
The industry must also be cognizant of the misconception of workers wearing some type of personnel protective equipment (PPE), which by default, means they can work on any equipment while energized. That could not be further from the truth. OSHA and NFPA allowances for justified energized work are specific to only the three certain allowances we reviewed. NFPA 70 Article 130, Work Involving Electrical Hazards, contains requirements for when justified energized work is going to be performed. Article 130 includes information associated with items such as an energized electrical work permit, shock risk assessment, arc flash risk assessment, approach boundaries, and PPE.
OSHA 1910, General Industry Regulations, Subpart S and OSHA 1926, Construction Industry Regulations, Subpart K both addresses electrical safety requirements that are necessary for the practical safeguarding of employees in the workplace. OSHA 1910.331 and OSHA 1926.416 are safety-related work practice sections that correlate with NFPA 70E requirements. Most of the other text in both subparts is language extracted from the NEC, but keep in mind that OSHA does not update it’s guidelines on a three-year basis as NFPA does. Although it has the ability to update it’s guidelines as needed, some have not been updated in years while others have not updated in decades. This results in OSHA guidelines sometimes being slightly behind the times when compared with other national consensus standards.
Personal Protective Equipment
Now let’s take a brief look at personal protective equipment for readers to have a direction for researching more detailed information. Starting at the top, head protection. OSHA 1926.100(a) requires protective helmets to be worn by employees when there is a possible danger of head injury from impact, or from falling or flying objects, or from electrical shock and burns. Hearing protection is required in accordance with OSHA 1910.101 and 1926.52 Table D-2 Permissible Noise Exposures, which is based on duration and dBA sound levels. OSHA 1910.136(a) addresses foot protection and requires that employees use protective footwear when working in areas where there is a danger of foot injuries due to falling or rolling objects, or objects piercing the sole, and when employee’s feet are exposed to electrical hazards.
![Infographic: PPE Equipment [Blue chart].](jpg/2020_05_vince_nfpa70_infographic-765x1024.jpg)
NFPA 70E Section 130.7(C)(6), PPE Body Protection, requires arc-rated clothing for employees when there is possible exposure to an arc flash that will produce enough energy to expose them to a second-degree burn, which is expressed as 1.2 cal/cm2. There are four different arc flash PPE categories associated with clothing, and other PPE, based on the hazard. This results in multiple considerations that must be taken into consideration for the proper selection of clothing. For example, one method is to use the NFPA 70E Section 130.7(C)(15) Arc Flash PPE Category Method. Using this method then requires Table 130.7(C)(15)(c) to be used for the selection of proper PPE. A high-level overview of the table shows that Arc Flash PPE Category 1 requires a minimum of 4 cal/cm2 arc-rated clothing, Category 2 requires a minimum of 8 cal/cm2 arc-rated clothing, Category 3 requires a minimum of 25 cal/cm2 arc-rated clothing, and Category 4 requires a minimum of 40 cal/cm2 arc-rated clothing.
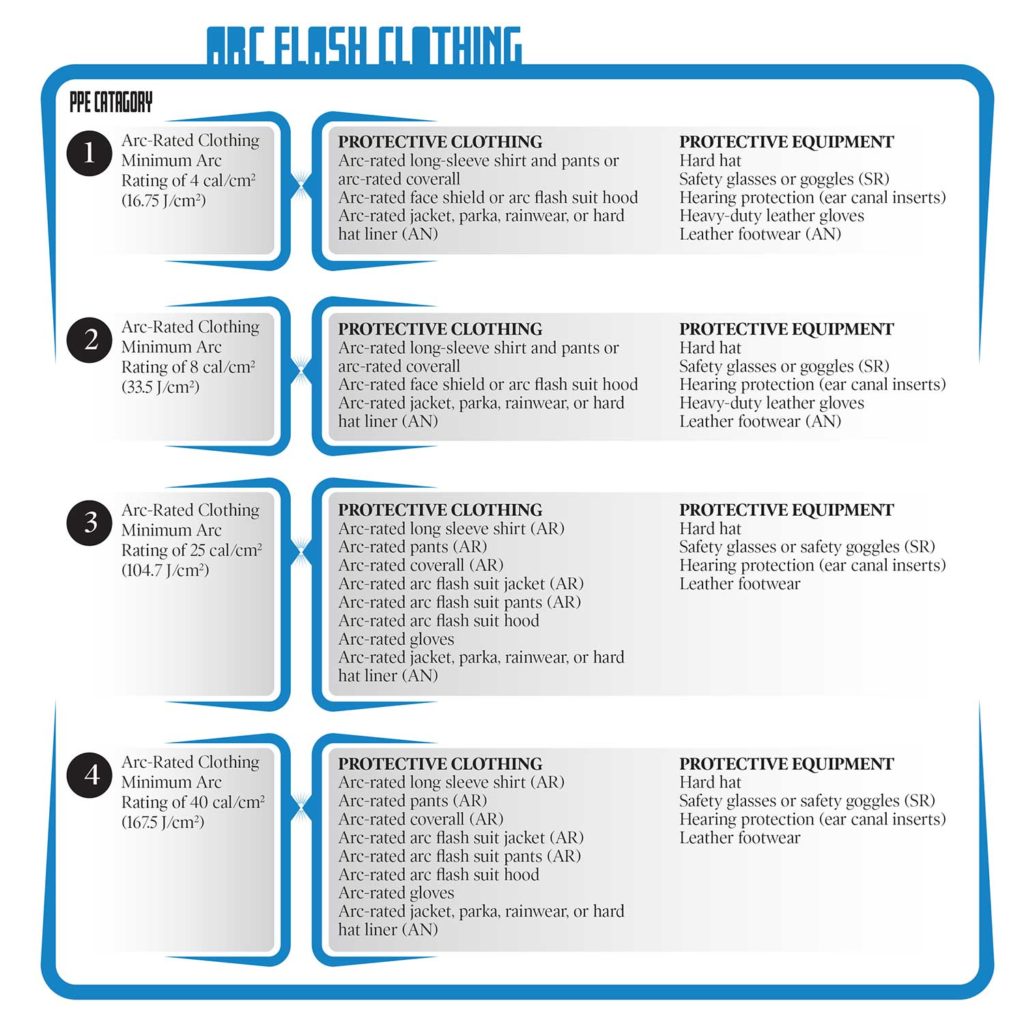
The “2-man rule.”
The last OSHA reference I want to highlight is the so-called “2 man rule,” which sometimes comes up in safety-related discussions. This information is located in 1910.269(l)(1). It requires that at least two employees be present during five specific conditions, all of which are relevant to over 600-volt installations.
- The first is for the installation, removal, or repair of lines energized at more than 600 volts.
- Second is the installation, removal, or repair of deenergized lines if an employee is exposed to contact with other parts energized at more than 600 volts.
- Third is the installation, removal, or repair of equipment, such as transformers, capacitors, and regulators, if an employee is exposed to contact with parts energized at more than 600 volts.
- Fourth is work using mechanical equipment, other than insulated aerial lifts, near parts energized at more than 600 volts.
- Fifth is other work exposing an employee to electrical hazards greater than or equal to those posed by operations that are specifically listed in the first four conditions.
There are however three exemptions to these requirements.
- The first exemption is for routine circuit switching if the employer can demonstrate that conditions at the site allow this work to be performed safely.
- The second exemption is for work performed with live-line tools if the employee is neither within reach of nor otherwise exposed to contact with energized parts.
- The third exemption is for emergency repairs to the extent necessary to safeguard the general public.
Summary
We’ve reviewed some background concerning the birth of OSHA and a handful of its safety guidelines. We also scratched the surface of NFPA 70E and reviewed only a small amount of its electrical safety requirements. OSHA has, for example, 10- and 30-hour training courses that provide attendees detailed information on its guidelines. Similarly, NFPA has multi-day training workshops that take a deep dive into NFPA 70E requirements. I encourage everyone to look into additional safety training not only to benefit themselves but to benefit their co-workers as well. Safety is a team effort and more collaboration equates to more people going home at the end of the day in the same condition as when they left in the morning.
Just as codes and standards continue to be revised and developed, so does OSHA and its guidelines. They’ve experienced growing pains just as any other agency or business has as it matures. Our industry will continue to change and evolve also. In order for all of us to return home safely every day, we must accept change, focus on workplace safety, have a continuous dialogue related to electrical safety, and embrace technologies and ideas that move safety forward.
Refernces
- NFPA 70E®: Standard for Electrical Safety in the Workplace®, 2018 edition. Copyright © 2018, National Fire Protection Association. For a full copy of NFPA 70E, please go to www.nfpa.org.
Find Us on Socials