Technicians often have an “Anything Goes; It’s Temporary” attitude about grounding, bonding, when dealing with the installation of temporary electrical systems and generators on construction sites, industrial facilities, special event venues, and disaster support sites. Electricity doesn’t distinguish between permanent or temporary installations. That’s why proper installation practices and workmanship apply to both. The main purpose of grounding and bonding is safety, yet the terms grounding, bonding, and grounded and their respective purpose are frequently misunderstood and misused in the field. This is especially true for portable and vehicle, including trailer-mounted generators. This short article discusses the purpose of system grounding, grounding requirements, separately derived systems, and available short-circuit current. Hopefully, it will clear up any misunderstandings or confusion surrounding the grounding and bonding of vehicle-mounted (trailer) mobile generators.
System Grounding
The purpose of system grounding is to intentionally connect one system conductor as the “grounded conductor” which is typically a neutral of an electrical system to earth in a manner that controls voltage with respect to the earth within predictable limits. The equipment grounding conductor(s) (EGC) are also connected to earth by the same grounding electrode conductor so the potential on the EGC is maintained the same as the grounded (neutral) conductor. The connection of the grounded (neutral) conductor to the EGC provides for the “effective ground-fault current path” to the source such as a generator. Grounding (connecting) to earth through an approved grounding electrode or grounding electrode system [example: ground rod(s)] as described in the 2017 National Electrical Code (NEC) Section 250.52(A)(1) through (A)(8) serves an important function within the electrical system.
The electrical system is intentionally grounded (connected) to earth in a specific manner to limit the voltage imposed by direct or indirect lightning strikes, line surges, or unintentional contact with higher voltage sources. The earth connection is also utilized to stabilize the voltage to earth during normal operations [250.4(A)(1)]. Earth or ground potential is usually considered zero or near zero. When there is a potential difference in charges between two points in an electrical circuit expressed in volts, current flow in the circuit will occur. Connecting to earth and creating a zero reference or zero potential difference eliminates touch potential between conductive surfaces and the earth in theory but is still based on the contact resistance of the earth connection.
The earth is not intended to be used as an effective ground-fault current path for fault detection and/or as a means of operating the overcurrent protection device (circuit breaker or fuse) to clear faults. The earth is conductive to a certain extent, but because of soil resistivity, it should never be considered as an effective path for ground-fault current [250.4(A)(5)]. If a ground-fault should occur, the current will return to the supply source on any available path with the majority going through the path of least path of resistance, which is the purpose of intentionally creating a low impedance path back to source through equipment grounding and bonding. Proper bonding of equipment intentionally creates an effective path for ground-fault current to travel back to the source to operate the overcurrent protective device (OCPD) effectively.
Grounding & Bonding Definitions
The following definitions are defined terms found in Article 100 of the 2017 edition of the NEC.
Bonded (bonding) is “connected to establish electrical continuity and conductivity.” This is accomplished when the joining of metallic parts together forms an electrically conductive path with the capacity to carry the anticipated fault current. Bonding is used to establish the conductive path for all electrically conductive materials and metal surfaces of a structure, studio equipment, lighting (520.81), tent frames (525.30), stage trusses and equipment not normally intended to be energized. Bonding is effectively interconnecting all conductive materials and surfaces together. In temporary applications, this is normally accomplished through the equipment grounding conductor (EGC), which is sized to provide a low impedance path back to the source to carry the anticipated ground-fault current and to avoid any appreciable potential difference between the parts [250.4(A)(3)]. Bonding provides a near-zero reference to eliminate touch potential between conductive parts if a ground fault should occur.
Ground. “The earth.” Note: The earth is not considered an effective ground-fault path per 250.4(A)(5).
Neutral Conductor is “the conductor connected to the neutral point of a system that is intended to carry current under normal conditions.” Examples of a neutral point would be a center connection on a single-phase, 3-wire generator or the common point on a three-phase, 4-wire, wye connected generator.
Grounded Conductor is “A system or circuit conductor that is intentionally grounded.” The connection can be to the earth and as permitted in 250.34 to the Generator Frame, with limitations, in place of the earth. The grounded conductor is sized in accordance with Table 250.102(C)(1).
System Bonding Jumper is “The connection between the grounded circuit conductor and the supply-side bonding jumper, or the equipment grounding conductor, or both, at a separately derived system.” The system bonding jumper provides electrical conductivity between the grounded (neutral) conductor and the equipment grounding conductor. The system bonding jumper is sized per Table 250.102(C)(1) and is based on the largest ungrounded phase conductor. Pay close attention to the notes listed at the bottom of the table. In portable or trailer-mounted generators, the system bonding jumper is typically located in the generator housing at the output lug panel (N-G terminals and to frame). The generator must be marked to indicate if the neutral is bonded or not per section 445.11 [see Article 445, Generators].
Equipment Grounding Conductor (EGC) serves a vital role in electrical systems, to simply characterize it performance it’s provides bonding, grounding and serves as an effective ground-fault current path. The EGC is used to connect the non-current -carrying metal parts of the system together with the system grounded conductor, the grounding electrode conductor, or both. The EGC provides a low impedance path back to source for fault current to flow to facilitate the operation of the OCPD should a ground-fault occurs. [See 250.4(A)(3) and 100 definition, “Informational Note 1; It is recognized that the equipment grounding conductor also performs bonding.” Types of acceptable EGC can be found in 250.118. The EGC is sized per 250.122 and based on the size of OCPD.
In a temporary and portable electrical distribution system continuity assurance of the equipment grounding conductors is critical. Each time the portable system is installed the continuity of the equipment grounding conductor must be verified per 525.32 (see Article 525, Carnivals, Circuses, Fairs, and Similar Events).
NEC Article 250 Part III explains the grounding electrode system and the grounding electrode conductor (GEC).
Grounding Electrode is “A conducting object through which a direct connection to earth is established”. The grounding electrode can be a metal underground water pipe, concrete encased electrode (rebar or copper conductor), ground ring, ground plate, and ground rod see 250.52(A). The most common grounding electrodes installed for temporary generators are the ground rods.
Grounding Electrode Conductor is “A conductor used to connect the system grounded conductor or the equipment to a grounding electrode or to a point on the grounding electrode system.” The grounding electrode conductor is used to connect the system grounded conductor or the equipment to a grounding electrode. The grounding electrode conductor is sized in accordance with 250.66.
Effective Ground-Fault Current Path is “An intentionally constructed, low-impedance electrically conductive path designed and intended to carry current underground-fault conditions from the point of a ground fault on a wiring system to the electrical supply source and that facilitates the operation of the overcurrent protective device or ground-fault detectors.” The effective ground-fault current path is the intentionally constructed, low-impedance electrically conductive path designed to carry ground-fault current from the point of fault back to the source to open the circuit OCPD to clear the fault before extensive damage occurs [250.4(A)(5)]. See figure 1.
In temporary applications, when a generator is used as the sole source of power, it important to understand the term Solidly Grounded System. A generator grounded (neutral) conductor connected to the ground (earth) without inserting any resistors or impedance devices between the system and ground is considered “Solidly Grounded.”
Note: Special consideration must be given to supplying power to temporary and/or portable concession trailers, stages, or tent structures. Bonding is required for metal raceways, metal enclosure for temporary electrical panel, metal frames, and metal parts of portable structures, trailers, and trucks per 525.30. This includes tent frames. Tents are considered portable structures per Section 525.1 [see Article 525 entitled Carnivals, Circuses, Fairs, and Similar Events]. Per Section 525.31, all equipment to be grounded shall be connected to an equipment grounding conductor of a type specified by 250.118.
Don’t forget the 12-foot rule per Section 525.11. Where multiple power sources or separately derived systems or both supply power to portable structures (tents) and are separated by less than 3.7 m (12 ft), the equipment grounding conductors of all power sources that serve the structure shall be bonded together at the portable structures. Prime example: one generator supplying 120/208-volt low voltage distribution to the tent, and another generator is running at 480 volts supplying power to HVAC equipment for the tent within the same proximity.
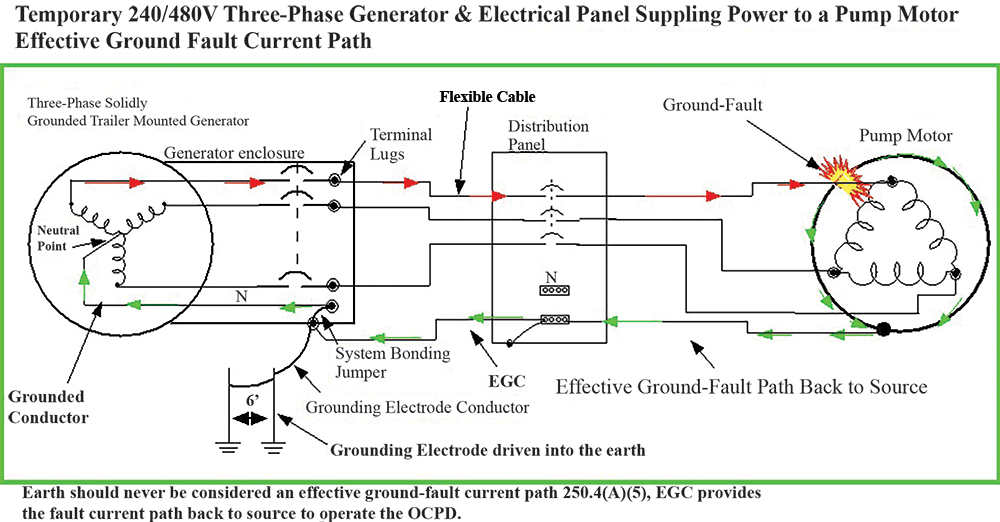
Grounding Electrode System & Grounding Electrode Conductor
Pay attention to Sections 250.52, 250.53, and 250.66; these sections intertwine with each other and can be misinterpreted.
Example 1: Grounding electrode conductor is sized per table 250.66 except as permitted in 250.66(A) through (C). If the grounding electrode conductor connects to a rod, pipe, or plate and does not extend to other types of electrodes, then the grounding electrode conductor does not have to be larger than a 6 AWG copper wire 250.66(A).
Example 2: 250.53(A)(2) a single rod, pipe, or plate electrode shall be supplemented by an additional electrode of a type specified in 250.52(A)(2) through (A)(8) which basically means when a generator is considered separately derived, and a ground rod is required then you have to install two or more. One must read the exception listed at the bottom of 250.53(A)(2): “Exception: If a single rod, pipe, or plate electrode has a resistance to earth of 25 ohms or less, the supplemental electrode shall not be required.” If a supplemental rod is required, they shall not be less than 6 feet apart [250.53(A)(3)]. Note: one conductor terminates on each ground clamp unless the clamp is listed for multiple conductors 110.14(A). See figure 2 for an example of a generator connected to earth using ground rod electrodes. Note that ground rods are to be fully driven to achieve the 2.44 m (8 ft) contact with the earth. From reference to Figure 2, we can assume the installer has installed two 8 ft 6 in. ground rod(s). The end of the ground rod does not need to be left above grade for the inspector to view. See 250.53(G).
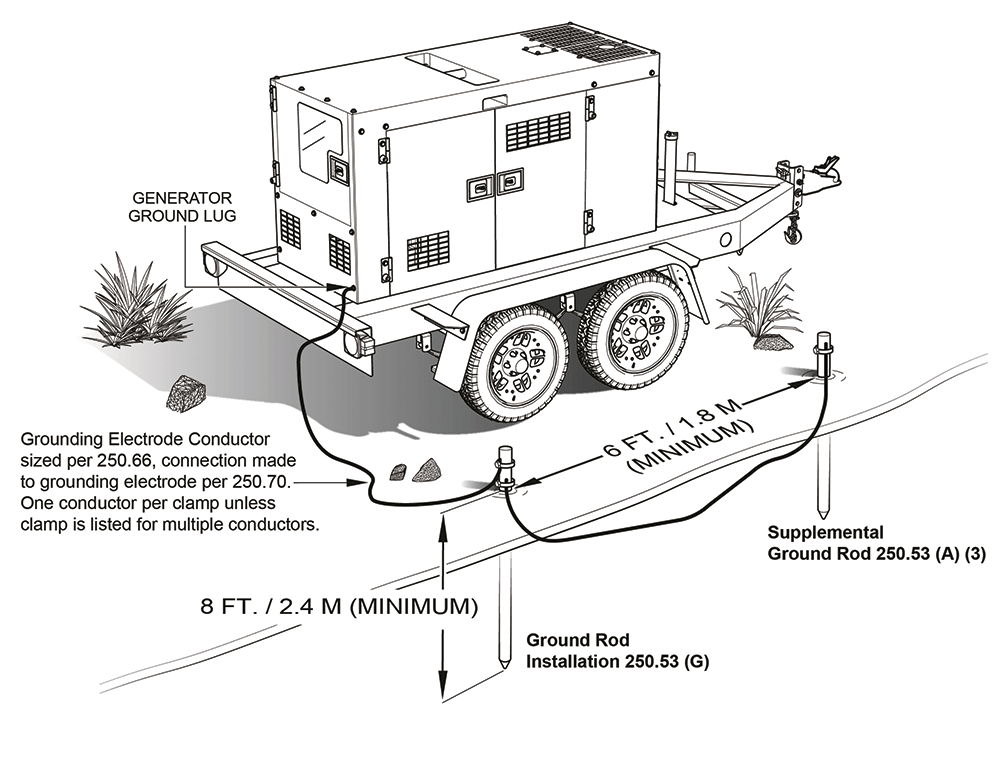
Separately Derived System
Separately Derived System is “an electrical source, other than a service, with no direct connection(s) to circuit conductors of any other electrical source other than those established by grounding and bonding connections”.
If a generator is the sole source of power for a temporary power distribution system, then by definition it is a separately derived system. If a temporary generator is used as an alternate source of power to a building service, then how the grounded neutral conductor is connected will determine if the generator is a separately derived system or not. If the transfer switch is designed to switch the neutral conductor (4-pole switch in a 3-phase, 4-wire system) in addition to the phase conductors, it would make the generator a separately derived system and must be grounded per 250.30. The generator is required to be field marked to indicate whether or not the neutral is bonded per 445.11. See Article 445, Generators.
Many temporary generators installed to supply power to a building service though a pre-existing transfer switch during disasters are not normally considered a separately derived system. The electrician must verify how the neutral conductor is connected in the transfer switch and service panel prior to the installation of a temporary generator.
If the neutral conductor is not switched in the transfer switch (3-pole switch in a 3-phase, 4-wire system) and it is connected directly to the service neutral grounded conductor, then the generator is not a separately derived system, and the requirements of 250.30 will not apply [see figure 3].
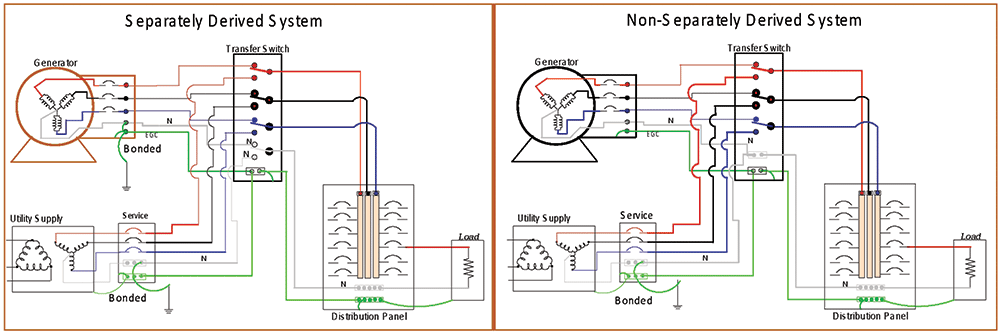
Note: Improper neutral to enclosure connection such as load side bonding and/or if both the transfer switch and generator have a solidly grounded neutral, can result in a potential for the flow of objectionable current on metal parts and the equipment grounding conductor [250.142]. This can also create parallel paths for fault current to travel. This affects the amount of fault current generated, which could cause improper operation of the OCPD.
Grounding Portable And Vehicle Mounted Generators
Per 250.34(A) and (B), portable and vehicle-mounted generators are not required to be connected to earth as long as the neutral point is connected to the EGC and the frame of the generator, and the generator only supplies equipment or receptacles installed on the generator (frame serves as grounding reference). Figure 4 shows an example of power supplied to temporary electrical distribution panels from the receptacles of a generator which would meet the requirements of 250.34 (A) and (B).
If the conductors to temporary electrical panels in figure 4# were hardwired into the generator lugs then it would not meet the requirement of 250.34.and the generator would be required to be grounded to the earth in accordance with 250.30. The authority having jurisdiction (AHJ) [which could be the electrical inspector, building official, fire chief, facility engineer- see definition of AHJ in Article 100] can still require a single and supplemental ground-rod(s) to be driven at the generator. Please consult your local AHJ before the start of a project to determine if system or equipment grounding connection to earth is required.
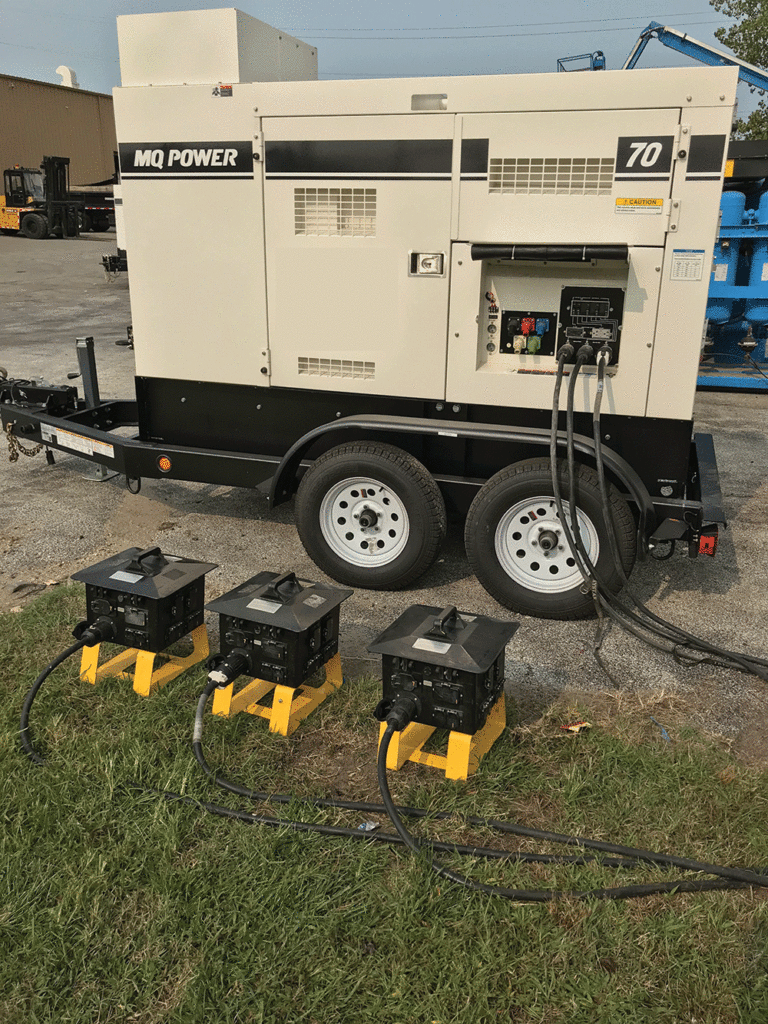
Ground-Fault Current & Overcurrent Protection
Special consideration must be given to the magnitude of fault current that can be generated within an electrical system to ensure the low impedance ground-fault current path can rapidly generate enough current to open the OCPD plus be cable of handling the current imposed to minimize damage. The higher the fault current value, the shorter the clearing time.
Available Fault Current in a temporary system is influenced by several factors such as transformer impedance, conductor material, size, length, motor-operated equipment, and other connected equipment, just to name a few. If a generator supplies power, the available fault current is relatively low compared to utility or a transformer. Generators produce rapid decaying fault current due to their impedance and reactance, which must be given consideration.
The characteristics of a generator are significantly different from transformers. Generators have little ability to withstand the sudden heating effects and mechanical stress of ground-fault current. Unlike a transformer, the three sequence reactances (positive, negative, and zero sequences) of a generator are not equal, with zero-sequence having the lowest value. Generally, if the generator has a solidly grounded neutral, it will have a higher ground-fault current than a three-phase fault current. The negative-sequence current thermal withstand limit is a product of time, and with a solidly grounded neutral, the ground-fault current can be about eight times that of full-load current while the three-phase fault current is about three to six times full load current. See figure 5. The fault current in the circuit was calculated based on the methods and formulas listed in Cooper-Bussmann’s. “A Simple Approach to Short Circuit Calculations.” The example shows how much current is calculated and how much fault current is available from the generator as a comparison.
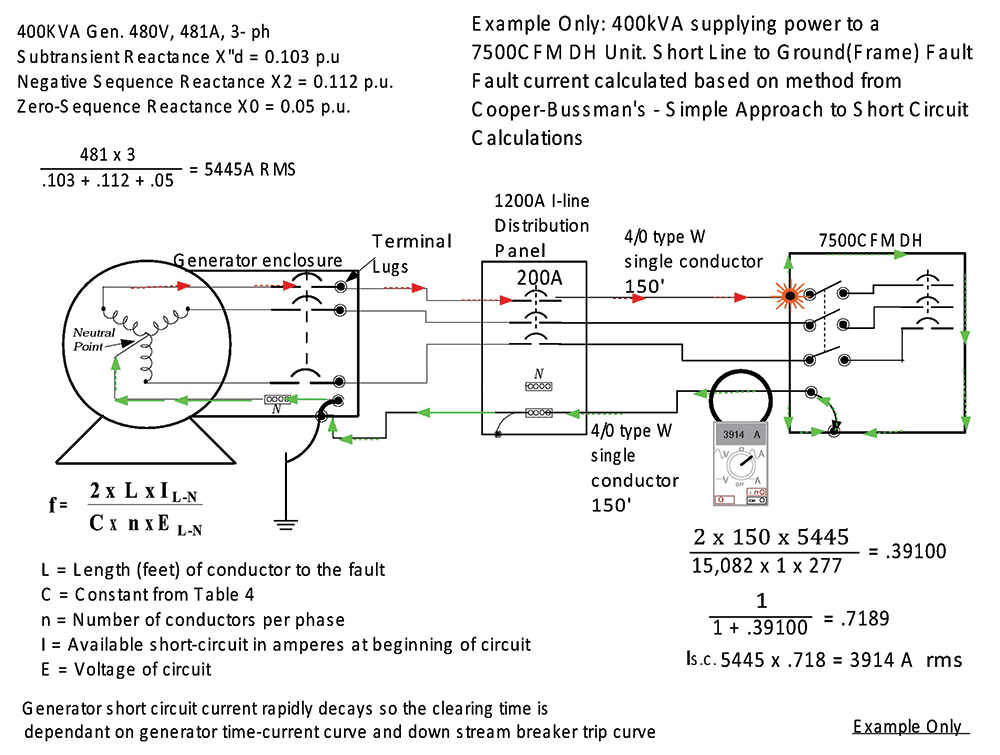
More and more I see low voltage rental generators in the range of 125 to 500 kVA used in parallel/power management applications due to the lack of larger engines that meet tier 4 final emission requirements [see EPA Standard, Final Rule for Control of Emissions of Air Pollution from Nonroad Diesel Engines and Fuel]. See figure 6 for an example of five 220 kVA generators operating in parallel/power management at a water treatment facility.
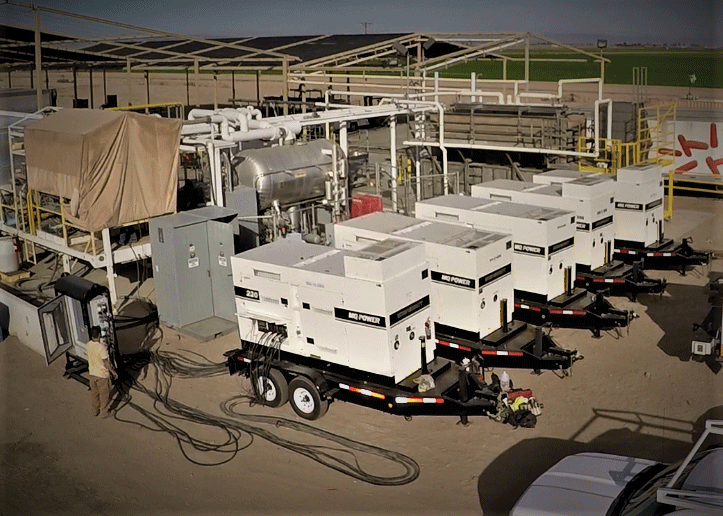
Generators operated in parallel can create a challenge for calculating fault current (see figure 7). The fault current is multiplied by the number of units operating in parallel at the time of the fault. Because of the damaging effects of ground-fault current on generators windings, some applications may require ground-fault detection and fault limiting high impedance grounded neutral systems, usually a resistor that limits ground-fault current to a lower value. The NEC allows these types of grounded neutral systems for voltages up to 1000 volts per 250.36.
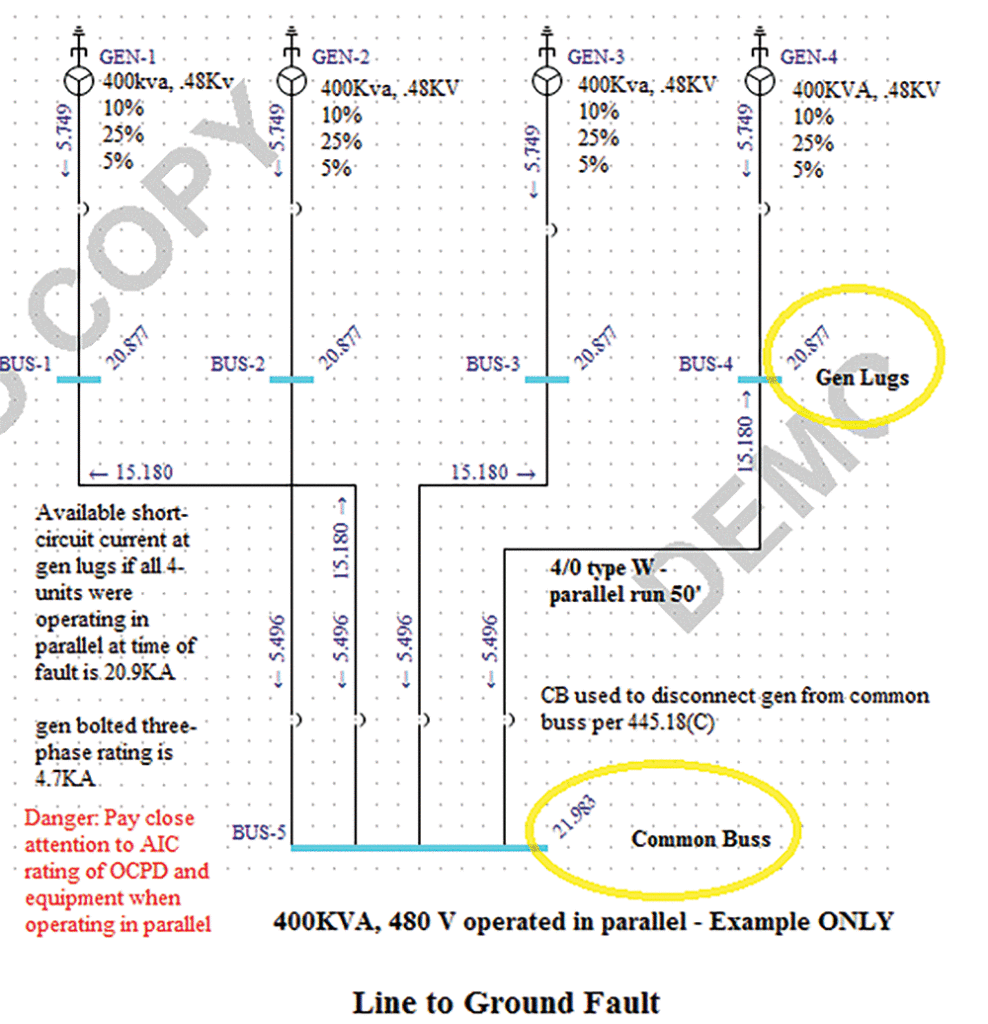
For systems over 1000 volts [see 250.187], when considering the use of fault limiting grounded neutral systems, I recommend you first consult with a professional engineer who specializes in these components.
References
IEEE Std 142 (2007) IEEE Green Book; Recommended Practice for Grounding of Industrial and Commercial Power Systems. IEEE Standards, Piscataway, NJ.
Pfeiffer, J.C. (2001) Principles of Electrical Grounding. Pfeiffer Engineering Co. Inc.
NFPA 70 (2017) National Electrical Code. ISBN: 978-145591277-3, National Fire Protection Association. Quincy, MA
Waterer, F. (2012). Effective Bonding and Grounding: The Backbone of Electrical Safety. Plant Engineering. Downers Grove, IL
Bulletin EDP-1 (2004) Engineering Dependable Protection For an Electrical Distribution System, Part 1, A Simple Approach to Short- Circuit Calculations. Cooper-Bussmann. Retrieved from; http://www1.cooperbussmann.com/library/docs/EDP-1.pdf
Find Us on Socials