Introduction
Nothing captures people’s attention more than something that can put on a good show. Add fire or explosions and people will give you all their attention. Therefore, it is not surprising why the industry gives its complete focus on electrical safety to arc flash. It is so much of a showstopper—with its 19,400 °C (or more) of heat that can destroy a business and the lives of anyone who stands in its path in just a tenth of a second. Arc-flash safety is important, however, the electrical industry’s deadliest act—electrical shock—is often left forgotten.
More than 90% of electrical fatalities among US workers are due to electrical shock. This number does not even account for the large proportion of injuries and fatalities that are often misclassified under a different cause of death. And yet shock is downplayed within industrial settings. Most electrical safety training programs don’t cover shock. Workers during production usually don’t exercise precaution against it, at least not enough to cut the power before proceeding to work safely. The NEC does not have shock protection requirements for all environments where lives are at risk.
Oftentimes, companies’ safety methods primarily focus on providing workers with PPE and safety training, which they assume makes them safe from any incidents occurring. However, PPE is considered the last line of defense on the hierarchy of controls, with safety training (which is an “administrative control”) falling next in line. A last line of defense is a last resort, and thus for companies to devote their resources to using last-resort protection methods, the disproportionate rate of worker fatalities that occur from electrical shock each year comes to no surprise.
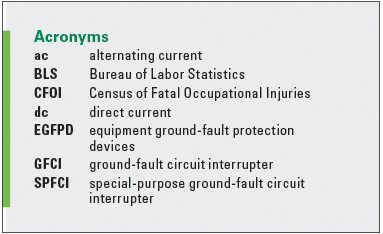
What Makes Electrical Shock So Dangerous
An electric shock is a sudden violent response to electrical current flow through any part of a person’s body.
Even minor shock injuries can result in life-altering and debilitating symptoms. Electrical shocks can cause long-term injuries with both neurological (such as loss of balance, poor coordination, and neuropathy), psychological (fatigue, irritability, and depression) and physical symptoms (such as muscle spasms, reduced range of motion, muscle aches, and joint stiffness) [1], [2].
Potential long-term consequences of electrical injuries may include neurological (e.g., neuropathy, seizures, syncope, tinnitus, paresthesias, weakness, loss of balance, poor coordination, or gait ataxia), psychological (e.g., memory or attention difficulties, irritability, depression or post-traumatic stress), ocular (e.g., cataracts) or physical (e.g., pain, fatigue, contractures, muscle spasms, pruritus, headaches, fever or night sweats, and reduced range of motion or stiffness in the joints) disturbances.
Resistance
It is the current—not voltage—that kills. Many factors contribute to the amount of current that enters the body, which is why a lower voltage does not indicate safety.
More than 99% of the body’s resistance to the flow of electrical current is at the skin [3]. Skin’s resistance becomes far less protective against electrical currents when:
- there is a breakdown of skin at 500 volts or higher;
- the skin is damaged through way of cuts, abrasions, or burns;
- it is immersed in water; or
- there is a rapid application of voltage to an area of the skin [3].
The human body, which is composed mainly of water, has a very low internal body resistance, between approximately 300 Ω and 500 Ω. The skin has a much higher resistance. The dryer the skin is, the higher its resistance will be. A calloused hand will typically have a resistance of around 100,000 Ω due to the thick outer layer of dry dead cells at the skin’s surface [3].
There are many factors that may cause a person to have a lower body resistance. A person with sweaty hands, for example, will have a lower body resistance and can be electrocuted at a lower voltage than what would otherwise be nonlethal.
Abrasions on the hand allow the current to bypass the skin resistance. The skin acts similar to a capacitor—it allows more current to flow when a voltage rapidly changes. If a person’s hand is holding a metal tool that suddenly touches a voltage source, the rapidly changing voltage will be applied to the person’s palms and fingers. If this happens, the current amplitude within the body will be significantly higher than would otherwise occur [3].
Above 500 V, high resistance in the outer layer of the skin breaks down, which greatly lowers the body’s resistance to current and thus increases the flow of current. What’s important here is that areas of skin breakdown are sometimes pinhead-sized wounds that can be easily overlooked. These tiny openings can enable a large amount of current to enter the body. This current typically results in deep tissue injury to muscles, nerves, and other structures. This is one reason why there is often significant deep tissue injury and little in the way of skin burns with high-voltage injuries [3].
![Figure 1. Number of US electrical fatalities began to flatline across the last decade [13].](jpg/2020_11_littelfuse_fig1.jpg)
The Let-Go Threshold: The Line Between Injury And Death
The let-go threshold is when a person is experiencing an electrical shock and loses their ability to let go of the object. This can oftentimes make the difference between life and death. Alternating current (ac) repetitively stimulates nerves and muscles that cause sustained contraction onto the muscles. These contractions onto the muscles do not stop so long as there is contact with the object. When a person’s muscles contract, their grip tightens. Once the current passes through the heart, fibrillation, resulting in brain damage and eventual cardiac arrest, is likely.
Why Electrical Shock Incidents Are More Serious Than The Data Reflects
No one is immune to dying from an electrical incident, regardless of their qualifications. According to data from OSHA, 64% of all electrical fatalities occur in non-electrical occupations [9]. Thus, companies still have a high risk of fatal incidents from electrical shock occurring regardless of any requirements for electrical work to be done by only qualified workers. Accidents happen.
Electrical injuries are particularly underrepresented in occupational injury and fatality data because they often become classified as a different type of incident. For example, if a worker is electrically shocked while using a ladder to change a light fixture and then falls from the ladder, the fatality is classified as being due to a fall, not electricity.
Another reason the industry lacks awareness of the prevalence of worker electrical fatalities is due to little-known inconsistencies between OSHA and the Bureau of Labor Statistics (BLS) data sets.
Of the worker electrical fatalities that occurred between 2011 and 2017, OSHA’s data sets only included 74% of those reported by the BLS Census of Fatal Occupational Injuries (CFOI) [5].
The CFOI data, however, cannot be used by researchers to understand the context behind these incidents because BLS’ separates the information surrounding the incidents into separate reports, rather than provide a single comprehensive set of data like that of OSHA. For example, the 2018 CFOI includes a data set that will tell us how many workers died due to electricity and another set for the number of fatalities among electricians, but because they are separate sets, we cannot determine how many of the electricians died due to electricity. This lack of comprehensive data reporting prevents researchers from analyzing the data to understand the context of these incidents, such as whether a worker who died from a fall fell because they were electrically shocked, for example.
The perception that electrical fatalities are on a steady decline is somewhat a myth due to improper classifications of injury and fatality cause of death; how BLS presents its fatality data; and unaccounted incidents in OSHA’s injury and fatality data sets.
According to the US BLS 2018 CFOI, 20% of US fatalities in installation, maintenance, and repair occupations were due to falls, which is significantly higher than other occupations such as those in transportation and material moving (19%), production (9%), and farming, fishing and forestry (4%). In this same year, 18% of the deaths among electricians were due to falls, whereas falls accounted for only 12.5% of the rest of the workforce (excluding construction) [13].
Industry reports [4] say that electrical fatalities have steadily declined since NFPA 70E became required. However, this is no longer true: a 2-year sliding average of these rates finds that this trend nearly flatlined after the fatality rate dropped in 2007 (see Figure 1). In 2007, OSHA published 29 CFR Part 1910, subpart S, which was the first revision to OSHA’s general industry electrical standard in 25 years. The basis of the updates brought in NFPA 70E-2000 (the previous version used NFPA 70E’s 1979 edition) and updated safety design requirements for electrical installations (such as expanded requirements for GFCI protection of temporary wiring used for maintenance and repair purposes) [8].
Upon OSHA’s requirement for companies to follow these updated electrical safety designs, the number of electrical fatalities sharply dropped. This decline, however, has nearly flatlined since.
The number of reported electrical fatalities has not only stopped declining, including those due to direct exposure (see Figure 2), but are likely significantly more than what the BLS data reports:
Why do people still choose not to follow lockout/tagout procedures or wear PPE? While doing research a few years ago with data from the Bureau of Labor Statistics, I found falls were a leading reason for deaths in electrical incidents. I knew electrical workers as a group couldn’t be significantly clumsier than the general population, so further digging revealed the statistic was skewed by those who were replacing overhead lighting fixtures on live circuits without proper PPE while on a ladder [5].
Bingham [5] went on to question why this rate hasn’t continued to be reduced despite the time and energy companies have spent on human-based safety practices:
“Workers following safety-related work practice requirements, limiting the approach, learning the arc flash concept, and wearing proper personal protective equipment (PPE) has a significant effect on injury and death rates. But why haven’t these practices continued to reduce the deaths and injuries? Making it the employer’s duty to create an electrical safety program and making it enforced practice within companies should have had a greater effect than waiting for an incident that called OSHA in to penalize the company.”
![Figure 2. Electrical shock fatalities from direct exposure to electricity [13].](jpg/2020_11_littelfuse_fig2.jpg)
Most companies today have detailed and comprehensive safety policies, regular training in NFPA 70E, and regular safety meetings and logs:
“The occurrence of an electrical accident might seem impossible in this safety-conscious environment, but preventing electrical accidents requires more than policies and training – it requires utilizing safe work practices 24/7 without exception. A checklist indicating a worker has PPE is not a guarantee that the PPE will be worn and worn properly. Written electrical procedures are not developed for many troubleshooting jobs. A worker is often more focused on fixing the problem rather than navigating the gray area of selecting the most appropriate PPE for an undefined task [10].”
These researchers are right. Too many workers are injured or die each year due to electrical shock, and we must do better at preventing them from happening. Developing an awareness of how and why these incidents occur is the first step, and designing out the hazards using protective components like GFCI protection is the solution.
What The Littelfuse Survey Found
The Respondents
Littelfuse surveyed 575 people who work directly with electricity from Jan. 23 to Feb. 21, 2020. The respondents were spread across a variety of industries such as manufacturing, electrical maintenance and repair, and utilities. Their job roles included technicians, design and project engineers, maintenance electricians, electrical contractors, and managers (safety, plant, and purchasing).
About 70% of the people surveyed primarily work with more than 220 volts, and the other 30% mostly work with 220 volts or less.
The respondents represented a range of different sized companies: more than a quarter (29%) of the respondents work for companies that have 1,000 or more employees, followed by 21% who work at companies of only 1 to 19 employees. About three-quarters of the respondents work in the United States (64%) and Canada (9%).
A Shocking Paradox: Confidence in Ability to Recognize an Electrical Hazard and a History of Being Shocked
One of the most alarming results found by the survey is the prevalence of higher voltage shock incidents among workers.
Nearly 40 % of the respondents said they have been shocked by more than 220 volts while on the job, which was about half (51%) of the 78% who reported having been electrically shocked at any voltage (see Figure 3).
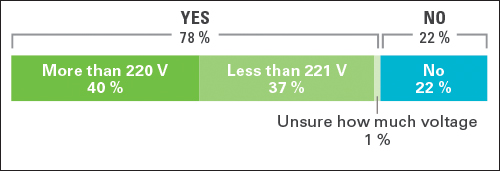
Q: Have you ever experienced electric shock while on the job?
Q: How confident are you in your ability to recognize an electrical hazard?
What’s interesting, is that most (86%) of the respondents who reported having experienced shock by more than 220 volts, also rated themselves as either “very confident” or “extremely confident” when they were asked to rate their ability to recognize an electrical hazard. This was significantly more than those who have never been shocked when on the job and slightly higher than those who reported having experienced shock from less than 220 volts (82%) (see Figure 4). Overconfidence was also frequently cited among respondents as the main reason for why people at their facility work on live equipment.
There was no statistical difference among those who have been electrically shocked at work and the size of their company. This was also consistent with the voltage range they primarily work with: 48% of those who work at companies with less than 20 employees work with 220 volts or less and 52% work with more than 220 V; 48% of those who work at companies with more than 1,000 employees work with 220 volts or less and 51% work with more than 220 volts (1% were unsure).
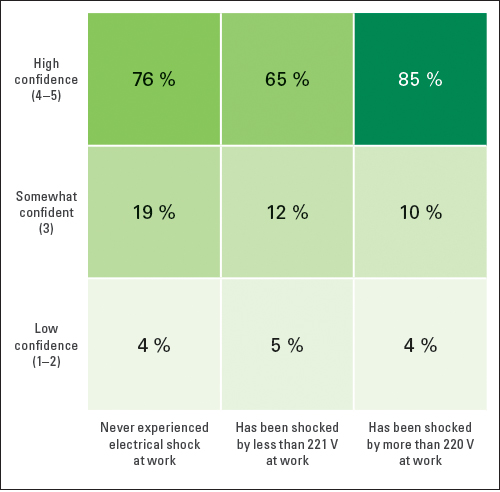
In the Heat of the Moment, Even the Best Safety Training Tends to Be Forgotten
More than two-thirds of the respondents said that workers in their facility perform work on energized equipment.
The survey asked respondents using an open-answer field to cite the main reason people at their facility work on energized equipment: troubleshooting was the most common justification respondents provided for working on energized equipment. The second most common rationale was for production purposes (such as to avoid the economic loss of stopping the equipment), followed by overconfidence, and reasons like laziness and convenience.
Larger companies (1,000 employees or more) were slightly more likely to have people work on energized equipment (66%) than companies with less than 20 employees (60%). The most common reason cited for doing so was the same for both groups: to maintain production and troubleshoot.
“At a large industrial site, equipment can range from a sophisticated production line to a simple light fixture. Workers may not realize that a cursory check of equipment exhibiting problems is not equivalent to a non-contact, visual inspection of equipment in good working condition” [6].
Workers often intend to just look, but in the context of determining the cause of the problem, this often cascades to a situation where the worker is suddenly troubleshooting energized equipment without proper PPE or safety protocol. Simple, quick fixes that change the nature of the work are easy to slip into. For example:
A worker troubleshooting a low-voltage control circuit might notice loose connections and decide to tighten those while the cabinet is open. This worker has failed to recognize that the nature of the task has changed. Tightening connections may require an energized electrical work permit, arc-flash and shock hazard analyses, management approval, two workers, and so on [10].
So why, despite having received electrical safety training from their company, had most of the respondents experienced electrical shock while on the job? As Gammon and Jamil said:
Electrical safety training often focuses on arc-flash hazards. Videos of arc-flash explosions and the images and stories of arc-flash survivors remain in the minds of trained electrical workers.
Unfortunately, electrical safety training rarely shows an interview of someone who has lost a loved one due to fatal electric shock or a person disabled from electric shock injury. Written safety policies prohibit work on live circuits, but workers sometimes fail to recognize the injury potential of troubleshooting/working on live lower-ampacity circuits or using electrical test equipment [10].
Q: What equipment voltage to ground do you consider safe to work on or near?
Let-Downs In Safety Training
When analyzing the results, it became very clear that not every facility’s safety training is working. For example, every respondent who cited PPE (or a form of it, such as gloves) as the main reason for why workers at their facility work on equipment while it’s energized also said they are provided electrical safety training by their workplace. If a worker believes they do not need to de-energize equipment if they wear PPE, then their safety training has failed.
Most alarmingly, among the respondents who cited PPE gloves and boots as the main reason for not de-energizing equipment before working on it also said:
- their facility does not send its electrical gloves to a laboratory for testing (which they are required to);
- they consider 550 volts or less to be a safe equipment voltage to ground to work on or near (their choices were a) less than 50 volts; b) less than 120 volts; c) less than 240 volts; and d) less than 550 volts).
Research indicates that “many workers who experience electrical injury have inadequate safety training to recognize safety hazards and follow proper procedures” [10]. Research found deficiencies in safety training that decrease its effectiveness and thus increase the likelihood of an electrical incident occurring, such as:
- the training misses important NFPA 70E topics;
- the training does not cover the current edition of NFPA 70E;
- the trainer is not qualified;
- the training is squeezed into one day;
- the training does not address the information that is pertinent for electrical workers to know [10].
Trainers have been observed to provide workers with faulty information such as to not to use rubber gloves when using live-line tools “because if your hands tingle, you know the tools are faulty”; storing rubber gloves in the incorrect bag class (which damages the gloves’ protective properties); and demonstrate how to test voltages at low-voltage motor control centers while wearing gloves that do not provide shock protection by ASTM requirements [10].
More than 50 volts of equipment voltage to ground is not safe to work on or near. However, when the survey asked the respondents how much equipment voltage they consider to be safe to work on or near, a quarter of the respondents believed more than 50 V is safe: 77% answered correctly; 9% believed up to 120 volts is safe; 5% considered up to 240 volts as safe; and 9% said 500 volts is a safe voltage.
Almost 90% of the those who considered 500 volts to be a safe equipment to ground to work on or near, also said their workplace provides them with safety training. Additionally, 62% of those who said they consider up to 500 volts to be a safe working voltage reported having experienced electrical shock by more than 220 volts while on the job.
The survey found no connection between an accurate knowledge of how much voltage is safe to work on or near (50 volts) and those whose company provides them with safety training (see Figure 5). In other words, the rate of safety-trained workers among those who considered more than 50 volts to be hazardous to work on or near was just the same as the rate of safety-trained workers who believed up to 500 volts to be a safe working voltage.
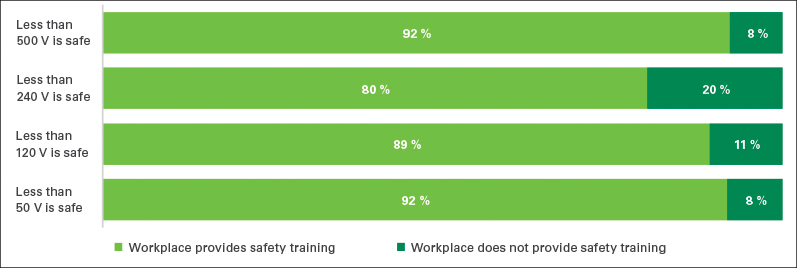
If a worker cannot distinguish a safe working voltage from a hazardous condition, then their safety training failed. It is also probable that any pertinent safety practices the worker has retained are ineffective when they are unable to read a hazardous situation.
A separate corporate case study examining electrical injury reporting and safety practices found that 40% of electrical injury incidents involved 250 volts or less and were indicative of a misconception of electrical safety as a high-voltage issue [7].
Most companies have well-established safety programs and provide safety training and PPE to their employees. And yet, almost 2,000 reported worker fatalities occurred in the United States between the sharp decrease in 2007, when CFR Part 1910, Subpart S updated its electrical installation requirements, and 2018. The number of workers who died from electricity is likely much more than this couple thousand, as it does not include those incidents that resulted from an electrical shock but were classified as a different cause of death.
The volume of electrical injuries and fatalities that anchor the trend of declining electrical fatalities occurred under a different electrical safety climate and without the protection of today’s standards and codes. The steady stream of injuries and deaths that have occurred in the United States ever since “can be attributed to 1) well-intended electrical safety programs falling short in their implementation; and/or 2) workers failing to recognize the severe injury potential in a situation perceived as a low-level hazard” [10].
If safety training does not help to decrease the misconception that more than 50 volts is dangerous to work around, and if 40% of incidents involving 250 volts or less are due to this misconception, then it is a company’s responsibility to rely on safety by design, even where not required under NEC, and not safety training.
Even those principles taught in safety training that resonate with workers are often abandoned during business operations; companies usually emphasize safety in hypothetical situations, but not when the situation occurs in real-time.
Simply put: safety training does not guarantee safety. Electrical injuries and fatalities are one of the most preventable types of occupational injury and fatality, and yet they continue to happen. It is far more difficult to engineer-out the possibility of a construction worker falling from scaffolding. His or her best chance for safety should they fall is dependent on the reliability and precision of the human-based practices of PPE. Electrical hazards, however, can be eliminated using “hard-science” methods such as ground-fault circuit interrupters (GFCIs), which do not rely on the soft-based science of human-based behavior for them to work as hoped.
Haphazard PPE Practices
Most industrial sites require employees to wear PPE. However, standard-issue PPE does not protect from electric shock and electrical workers might be lax in properly wearing electrical PPE. Workers often complain electrical gloves make it difficult to get the job done because they are cumbersome or bulky1 [10], [11].
Electrical gloves are the least effective safety method under NFPA 70E hierarchy of controls due to the high level of human error that must be overcome for them to work. While absolutely important, electrical gloves are the last line of defense. Electrical gloves must maintain their dielectric properties, physical strength, flexibility and durability for them to remain effective. Whether the worker ultimately wears them is a different story.
Almost a quarter (23%) of the respondents said their facility does not send its electrical gloves to a laboratory for testing. Another quarter of the respondents said they were unsure if their facility tests them.
Safety is already at odds against shock hazards when PPE and training are the only hazard mitigations used by a company. To issue human-error prone workers PPE is important, but PPE that is simply assumed to be in working condition without it undergoing required testing is reckless. PPE is important, but it is not good enough.
Rubber insulating gloves are required by CFR 1910.137 – Electrical Protective Equipment to be tested by a laboratory every 6 months (as well as upon indication that their insulating value is suspect, after repair, and after use without protectors). Even gloves that have been electrically tested but never issued for service may not be used if they were not tested within the previous 12 months.
While these results were discouraging across the board, larger facilities of 1,000 or more employees were more likely than small companies to test their electrical gloves as required: among companies of 1,000 or more employees, 18% said their facility does not have its gloves tested (22% were unsure), while 38% of those at companies of less than 20 employees admitted their facility does not test its gloves (25% were unsure).
Companies sometimes use rubber mats to provide an additional layer of protection for workers. However, just like all other types of PPE, rubber mats do not eliminate the potential for injury and fatality incidents. Workers do not always use the mats due to the hassle of extra work they create when breakers or contactors are racked in or out. Rubber mats are also rendered ineffective when wet, which also causes workers to not use the mats [10]. In wet applications, a three-phase GFCI (which can be used with a cart for portability), is the optimal solution to protect against shock.
Why Safety By Design Matters
It is easy to defend that any of the bottom-hierarchy safety measures are the least effective methods of preventing injury and death. Yet people still rely on these methods as their first resort—which, though important, are supposed to be a last-resort method. PPE is required, ground-fault protection is not required for less than 1200 A and shock protection usually isn’t. This is not a reflection of their importance, it is a reflection of the American legislative process.
For example, the reason that electrocution incidents began to decline after the 1970s can be attributed to the implementation of the safety legislation and of the regulations of the Industrial Safety and Health Act and the Industrial Safety and Health Regulations that were established in 1972. In 1969, the installation of ground-leakage current circuit breakers became a requirement.
Overheard voltage-distribution lines that have insulated cables carrying voltages less than 6,600 volts have been prevalently used in Japan since they became required in 1965. In the United States, where there is a higher rate of electrocution than in Japan, insulated cables are not used. Companies could easily avoid these fatalities by replacing these lines with insulated cables, as used in Japan, but without a legislation in place mandating them to do so, protection against death is optional and as such, the fatalities continue forward [12].
The NEC does not require GFCI protection for all areas where shock hazards that can injure or kill a person exists. PPE, however, is always required whenever a shock hazard exists that can cause injury or death. And yet, PPE is the least effective preventative measure and responsible for many injuries and fatalities due to its human-based practices. GFCI protection, which is a much more effective preventative measure as it nearly eliminates the hazard, saves lives because it does not require human involvement for it to work. Its out-of-sight-out-of-mind practice requires zero energy from the workers for it to guarantee their safety.
Special-purpose GFCIs (SPGFCIs), which work in circuits running 208 volts to 600 volts, monitor the equipment ground conductor for continuity. The equipment ground ensures ground-fault current (in the case of a phase-to-ground fault) flows through the ground instead of through the human body. The equipment ground ensures the current flows through the ground instead of through the human body, which provides a low-resistance path.
As a reminder, it is the current, not the voltage that kills. This is why Class C, D, and E GFCIs are so important: they are responsible for monitoring the ground-return path continuity and then to interrupt power if any integrity is lost. This in turn eliminates the possibility of personnel from being shocked or killed.
Ground-fault circuit interrupters are not to be confused with ground-fault relays; ground-fault relays provide equipment protection, whereas GFCIs protect human life.
Insurance company findings and research has found that electrical injuries are among the costliest for the high medical and associated rehabilitative costs [9].
SPGFCIs are required to trip at a minimum of 1 s for 20 mA ground faults, which provides complete protection for the human body. Additionally, there is a low probability of injury from currents up to 50 mA that last up to 2 s with a GFCI, which is in the AC-3 zone (see Figure 6).
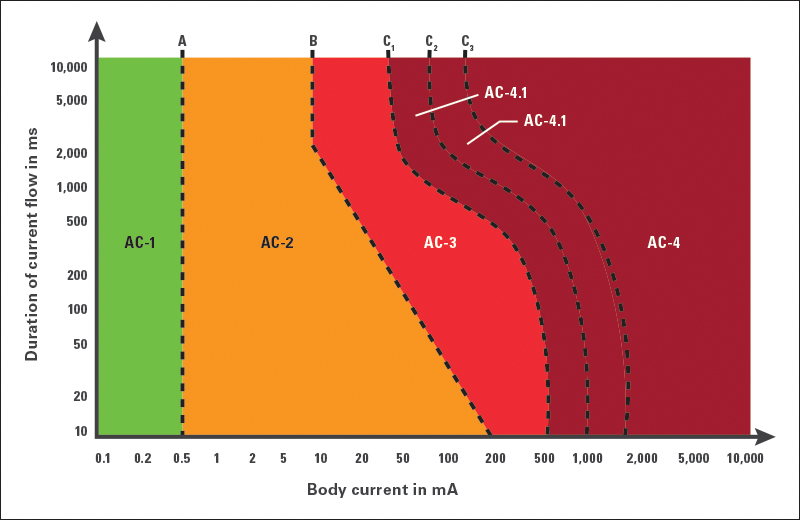
A GFCI monitors the difference between current in the phase conductors going out to the load and returning through those conductors. Any difference indicates that current is returning through an unintended path (usually through ground and potentially through a person), and when such a current is detected, the GFCI rapidly shuts off the power. A GFCI differs from a ground-fault relay in one vital aspect: a ground-fault relay does not open the circuit directly, but instead triggers an upstream circuit breaker or contactor to open. As a result, even the fastest and most sensitive ground-fault relays are not classified as people protection because the total interruption time is not tested by the manufacturer to conform to UL 943C. SPGFCIs monitor the ground conductor, and will trip if the ground conductor is discontinuous (when the load loses the low-resistance grounding path). This protects workers from an ungrounded chassis, which can potentially be at a full-phase voltage as a result of a ground fault.
The use of the acronym GFCI isn’t regulated, and while it implies personnel protection, not all products marketed as GFCIs are actually tested to protect people. Some of these products being marketed as GFCIs failed during testing, while others do not meet the applicable standards for personnel protection. Some even reference these standards in their marketing materials, which implies that they meet or exceed the requirements when they do not. For industrial personnel protection, look for the UL 943C Listed mark or the CSA C22.2 No. 144-M91 Ground Fault Circuit Interrupters, Class 1451-01 mark.
Until 2009, GFCI protection was limited to ac circuits up to 240 volts (150 volts line-to-ground), which are listed as Class A GFCIs in UL 943. However, because the hazards that GFCIs protect against extend beyond these applications, UL published UL 943C, which established three new classes of SPGFCIs for systems up to 600 volts. These SPGFCIs trip at 20 mA instead of Class A’s residential trip-level of 6 mA. This higher trip level provides a greater flexibility for an industrial application, while still tripping fast enough to protect workers and meet UL 943 requirements.
- Class C SPGFCIs are for use in circuits with a line-to-line voltage of 480 volts or less where reliable equipment grounding or double insulation is provided.
- Class D SPGFCIs are for use in 600-volt systems, and with specially sized, reliable grounding, which provides a low impedance path so that if a fault occurs, the voltage across the body will not exceed 150 volts. This protects the body from ventricular fibrillation, but not the let-go threshold.
- Class E SPGFCIs are for systems similar to class D, but with special high-speed tripping required that will eliminate the need for the oversized ground of Class D.
For some applications, 20 mA can be too sensitive (particularly if there are variable frequency drives present). Equipment ground fault protection devices (EGFPDs) are similar to SPGFCIs, but protect equipment instead of people, and can be used in these settings to help increase safety. EGFPDs operate on the same inverse time curve as other GFCIs as prescribed in UL 943 and UL 943C, but have adjustable sensitivity, typically from 6 mA to 100 mA. This enables the sensitivity to be adjusted to the next highest sensitivity that is above the base leakage current.
Doing so creates the safest possible conditions for workers in environments where worker protection at 20 mA is not possible. EGFPDs can monitor the ground conductor as well, but such monitoring is optional as it is not required by the standard.
Systems that have higher maintenance requirements are less forgiving of human error and more prone to failure. Again, the most commonly cited rationale provided by the survey respondents for working on energized equipment was maintenance and troubleshooting. Implementing GFCIs and other prevention through design components will not only save costs, but will save lives as well.
Human life is priceless, and the cost of an incident exceeds far beyond even the steepest of OSHA fines. Companies sometimes focus solely on the cost of compliance, but estimating costs should be framed in a way to consider the benefit of lives and dollars saved in the prevention of deaths, injuries, and property loss.
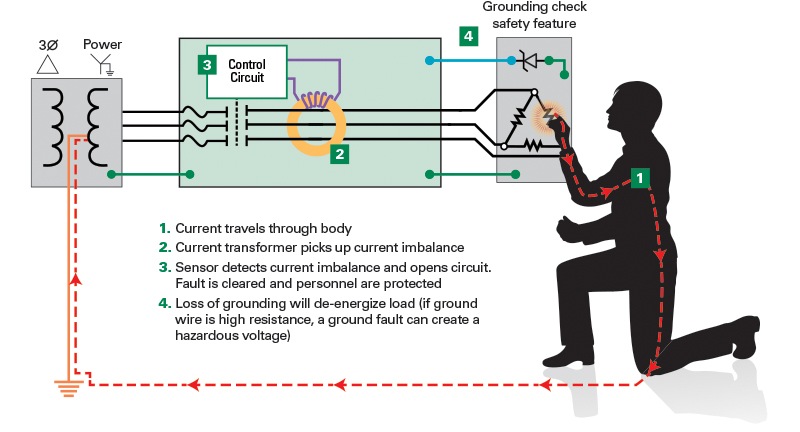
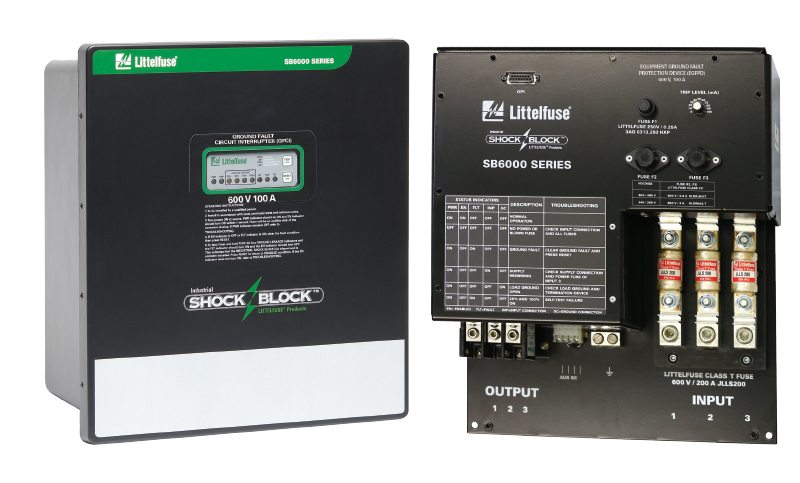
Conclusion
Only in the aftermath of tragedies is it easy to understand just how important investing in prevention really is. Human-based safety methods require them to be executed with consistent precision: without error, by every person, and every time. This is not possible because people make mistakes; it’s only human.
The survey results suggest that safety training isn’t working. If it were, workers would have a more accurate understanding of what makes an electrically hazardous situation, and shock injuries and fatalities would, at the very least, have leveled off over the past several years.
The NEC does not protect all workers from shock. The industry has the data to capture the changes desperately needed in the 2023 NEC and better align the new addition with NFPA 70E’s core message: human-based controls are an inadequate measure for ensuring safety.
For more information, visit Littelfuse.com/ShockProtection.
References
[1] M. S. Morse, “A report on the current state and understanding of human response to electrical contacts,” presented at the IEEE Industry Applications Society Electrical Safety Workshop, Dallas, TX, USA, Mar. 11–15, 2013, Paper ESW2013-05.
[2] M. R. Zemaitis, L. A. Foris, R. A. Lopez, et al, ”Electrical Injuries,” StatPearls Treasure Island (FL): StatPearls Publishing; 2020 Jan. Available from: https://www.ncbi.nlm.nih.gov/books/NBK448087
[3] R. M. Fish and L. A. Geddes, “Conduction of Electrical Current to and Through the Human Body: A Review,” Eplasty, vol. 9, no. 44, Oct. 2009. Accessed: Mar. 04, 2020, [Online]. Available: https://www.esfi.org/workplace-injury-and-fatality-statistics
[4] Workplace Injury & Fatality Statistics, Electrical Safety Foundation International, 2019. [Online] Available:https://www.esfi.org/workplace-injury-and-fatality-statistics
[5] R. Bingham. “Flatlining: The Decline in Electrical Fatalities Has Nearly Leveled.” Electrical Contractor.https://www.ecmag.com/section/safety/flatlining-decline-electrical-fatalities-has-nearly-leveled accessed (Mar. 13, 2020).
[6] T. Gammon, D. Vigstol and R. Campbell, “Workers at Risk of Fatal and Nonfatal Electrical Injuries,” IEEE Transactions on Industry Applications, vol. 55. no. 6, Nov./Dec. 2019.
[7] R. B. Campbell and D. A. Dini, “Occupational Injuries From Electrical Shock and Arc Flash Events,” Fire Protection Research Found. Quincy, MA, USA, Mar. 2015.
[8] Department of Labor, Federal Registrar, 29 CFR Part 1910, Subpart S. Available from:https://www.osha.gov/sites/default/files/laws-regs/federalregister/2007-02-14.pdf
[9] B. Brenner, J.C. Cawley and D. Majano, “Electrically Hazardous Jobs in the United States,” IEEE Transactions on Industry Applications, to be published. DOI 10.1109/TIA.2020.2980221.
[10] T. Gammon and S. Jamil, “The Disconnect Between Electrical Safety and Accident Prevention,” IEEE Industry Applications Magazine,” to be published.
[11] Industrial Accident Prevention Association and Ontario Women’s Directorate, “Personal Protective Equipment for Women – Addressing the Need,” The Center for Construction Research and Training, Silver Spring, MD, USA, Accessed on: Mar. 16, 2020. [Online]. Available:
http://elcosh.org/record/document/1198/d001110.pdf
[12] N. Ichikawa, T. Amano, and R. Nakata, “Human-Body Impedance and Electric Shock,” Journal of Biomedical Systems & Emerging Technologies, vol. 5, no. 2, 2018.
[13] Census of Fatal Occupational Injuries (CFOI), US Department of Labor, Bureau of Labor Statistics, 2019. [Online] Available:https://www.bls.gov/iif/oshcfoi1.htm
For more information, visit Littelfuse.com/ShockProtection
Disclaimer Notice – Information furnished is believed to be accurate and reliable. However, users should independently evaluate the suitability of and test each product selected for their own applications. Littelfuse products are not designed for, and may not be used in all applications. Read complete Disclaimer Notice at www.littelfuse.com/product-disclaimer.
Reprinted with permission from Littelfuse. Available online at Littelfuse.com/shock-survey-report
© 2020 Littelfuse, Inc.
Find Us on Socials