The increase in size of solar photovoltaic (PV) systems in recent years has made it more and more difficult to install the AC output into existing building panelboards, either at the electrical service location or sub feed panelboard locations. The basic reason for this is the restriction on not loading the panelboard bus assembly to more than 120% of its rating from a summation of all power sources. To compensate for this, many PV system designers and installers are utilizing National Electrical Code (NEC) allowances to connect energy sources ahead of the service or feeder disconnecting means. These allowances are covered at NEC Section 230.82 for services, which reads in part as follows “Only the following equipment shall be permitted to be connected to the supply side of the service disconnecting means: (6) Solar photovoltaic systems, fuel cell systems, or interconnected electric power production sources.” So, what constitutes a “service”? This question is answered in Article 100 for the definition of a service, which is simple: “Service. The conductors and equipment for delivering electric energy from the serving utility to the wiring system of the premises served.” As you can see, to be considered a service, the source of power must be a utility company distribution system.
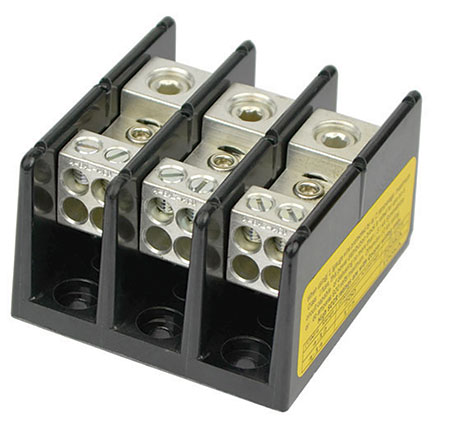
With that in mind, how are these installations sized and are there any other methods to interject premises on-site power sources into the electrical supply system? NEC Article 705, Interconnected Electric Power Production Sources, covers this. The first thing you will notice from the title of this article is that it applies to any on-site power source, not just PV systems.
Section 705.12 contains the prescriptive requirements for interjecting power sources from the output of the utility interactive inverter into the premises electrical system.
705.12(A) deals with connections ahead of, or on the supply side of, a service main disconnect. The requirements here are simple as the total of any overcurrent devices for the power production sources cannot exceed the rating of the service. The rationale here is that although the service disconnect will limit the current provided on the line side, the power production sources will send any additional current out into the utility grid. Because of this, the available current must not be more than the conductors can carry. There is also a concern here about available fault currents to which these conductors may be subject. Many people believe that PV systems can generate large fault currents like utility distribution systems do. That is not true as PV systems are power-limited; and if the conductors are properly sized, they will always be larger than the maximum current that the PV system can generate. The real concern with conductors from alternative energy systems that are connected ahead of the service disconnect is the potential for them to be exposed to fault currents generated on the utility side. To compensate for this, language was added in Section 705.31 of the 2014 NEC to limit the conductor length to 3 m (10 ft). There is also an exception allowing these conductors to be more than 3 m (10 ft). in length if they are protected at their point of connection to the service conductors by either cable limiters or current-limited circuit breakers. The other item to remember here is that many people are using power distribution blocks to make these connections. These are good products, but according to the UL product listing (see OPQS), these devices are rated 1000 volts or less, and in systems with available fault current of 10,000 amperes or less, unless labeled otherwise. The product standard also recognizes power distribution blocks for use on both the supply side and the load side of the service disconnect. However, if used on the supply side, power distribution blocks must be checked and verified that they are acceptable for use on the supply side (see photo 1). The NEC contains requirements for the use of insulating covers on terminal blocks.
Installers are also using a variety of connectors to make these connections with both the insulation piercing type and the threaded lug type (see photo 2). These connectors in photo 2 show just a couple of the many types being used. My research has shown that these types of connector are covered under UL 486 A/B, and they are limited to use at 600 volts or less. It also has shown that there are no evaluations on this type of connector for limiting the use ahead of the service main or fault current ratings. There are many factors to be considered when using this type of connector, the most important being that proper torque requirements in accordance with the manufacturer’s instructions are used. It is also important to follow the manufacturer’s instructions for using the connectors. Other NEC requirements to consider are such things as wire bending space, splices, taps and conductors in the cross section of a wiring space within a panelboard not to exceed 75% of that area (see 312.6).
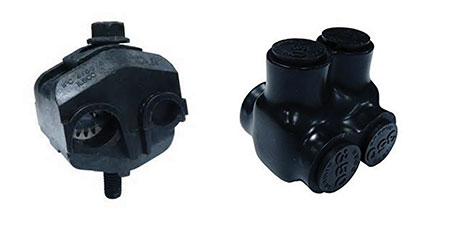
The other concern that arises here is what these conductors are called. Many want to identify these interconnection conductors as “Service Conductors.” To clarify this once again, let’s look at the definitions found in Article 100.
Service Conductors. The conductors from the service point to the service disconnecting means.
Service-Entrance Conductors, Overhead System. The service conductors between the terminals of the service equipment and a point usually outside the building, clear of building walls, where joined by tap or splice to the service drop or overhead service conductors.
Service-Entrance Conductors, Underground System. The service conductors between the terminals of the service equipment and the point of connection to the service lateral or underground service conductors.
When using these definitions, it is clear that these conductors do not meet the definition of “Service-Entrance Conductors” yet many interpret these to be service-entrance conductors. The following Exception to 230.40 adds further confusion to this:
Exception No. 5: One set of service-entrance conductors connected to the supply side of the normal service disconnecting means shall be permitted to supply each or several systems covered by 230.82(5) or 230.82(6).
It is my opinion that this exception is confusing and unnecessary, and I intend to submit a Public Input to change this in the 2020 NEC. I encourage anyone else who has concerns with this exception to do the same.
You may ask, “What is the big deal with what we call these conductors?” That is easy to answer. If these conductors were called service-entrance conductors, the installation would be limited to the wiring methods specified in 230.43. It is my opinion as a longstanding member of Code Making Panel 4 that these conductors should not be considered service-entrance conductors. As mentioned above, regardless of what these conductors are called, the two most important considerations are to be certain that (1) they are sized large enough for 125% of the inverter output current, and (2) that means to address any available fault currents are part of the installation.
Section 705.12(D) establishes requirements for connections made on the load side of the service disconnect. Some of these requirements in the 2014 NEC are the same as they have been in previous editions; however, there are some new and different requirements.
705.12(D)(1) remains predominately unchanged other than clarification that more than one inverter supply can be connected on the load side of the service disconnect of a building. Whether there is 1, or more than 1, they each must terminate in either a dedicated circuit breaker or fusible switch.
705.12(D)(2) deals with connecting into either feeder conductors or busbars, with some clarification on how feeders that are part of taps regulated by 240.21 are calculated. This section also establishes that for all the calculations listed, the ampacity rating of 125% of the inverter maximum output rating shall be used. If the connection is made into a feeder, the word connection is important here as many people call these taps; and they are not taps. The connection is made between the overcurrent device protecting the feeder and the load terminations the installation must meet one of the following requirements:
The feeder conductors must be large enough to carry the total ampere rating of the feeder overcurrent device and 125% of the maximum rated output current of the inverter(s) or
The feeder conductors terminate in an overcurrent device at their load end no larger than the ampere rating of the conductors.
When evaluating these two options, all the other requirements for properly protecting the feeder conductors and inverter output conductors must be considered and the calculations for continuous loading and conditions of use must also be evaluated.
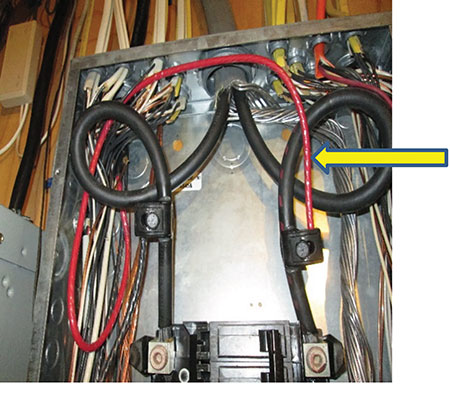
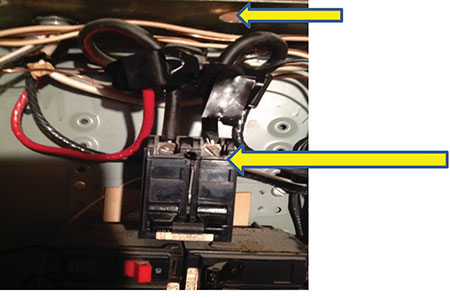
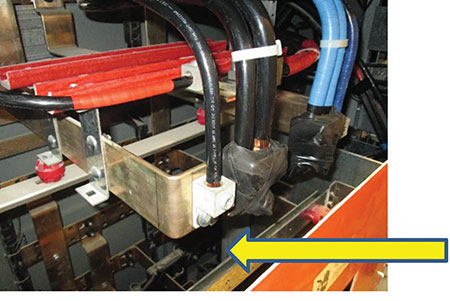
Part 2 of 705.12(D)(2) covers the requirements for taps that are connected to feeders that also support the connection of alternative energy sources. Again, as stated above, the connection of alternative energy systems into feeders are not the taps being addressed here as they are not taps. What is being addressed is a feeder tap that is made in accordance with 240.21 and the feeder also has an alternative energy source connected to it. In these cases, the sizing of the tap must be based on feeder overcurrent device and 125% of the inverter output rating. For example, if you had a 400-ampere overcurrent device protecting a feeder and you added an inverter output circuit with the maximum inverter output rating being 100 amperes. From this feeder, you are going to make a tap using the 7.5 m (25 ft) tap rule [see 240.21(B)]. These tap conductors would have to have an ampacity of at least 175 amperes, 525/3. The 525 amperes would be derived by adding the existing overcurrent device rating, 400 amperes and 125% of the inverter output, 100 amperes x 1.25 this equals 525 amperes.
In smaller systems, the most common method used for interconnecting alternative energy sources and utility power is through circuit breakers that are attached to panelboard busbars. There are a few different ways to accomplish this with the most predominant concern being that the busbars are not overloaded. The first bit of information needed for busbar connections is the maximum current rating of the busbars, which is usually found on the labels that the manufacturer installs within the panelboard. However, if there is any confusion, the manufacturer can provide actual information about the ratings of their products.
The first NEC requirement is in 705.12(D)(2)(3)(a), which is straightforward. If the combined rating of the overcurrent device for the feeder supplying the panelboard and 125% of the maximum inverter output rating do not exceed the busbar rating, the connections can be made anywhere in the panelboard.
The second NEC requirement, located in 705.12(D)(2)(3)(b), covers the very common practice of installing the two sources, feeder and inverter output, at opposite ends of the busbar. If this method is used, the combination of the feeder overcurrent device and 125% of the inverter output cannot exceed 120% of the panelboard busbar rating. For example, if you had a panelboard with busbars rated 225 amperes, the maximum total supplies cannot exceed 225 amperes x 1.2 or 270 amperes. This being the case, if the feeder was protected by a 200-ampere circuit breaker, the total inverter output could not exceed 70 (270, the 120% rating – 200 the feeder circuit breaker rating) times .8 (the inverse of 125%) or 56 amperes. This easy method can be used to figure the maximum amount of alternative power that can be fed into an existing panelboard.
A recent Tentative Interim Amendment (TIA) was passed to clarify that this same methodology can be used for a center-fed panelboard.
TIA 14-12
(SC 16-8-16 / TIA Log #1234)
- Add new 705.12(D)(2)(3)(e) to read as follows:
(e) A connection at either end, but not both ends, of a center-fed panelboard in dwellings, shall be permitted where the sum of 125 percent of the power source(s) output circuit current and the rating of the overcurrent device protecting the busbar does not exceed 120 percent of the current rating of the busbar.
Another thing to be cautious about when applying these requirements is the listed busbar rating of the panelboard. For example, when a panelboard is assembled by a manufacturer with 225-ampere busing and a factory installed 200-ampere circuit breaker is installed ahead of the busing, the bus rating may then be limited to the 200-ampere rating. The way to determine this is to look at the labeling inside the panelboard, contact the manufacturer, or the testing lab that listed the panelboard.
This article is focused on PV systems. However, Article 705 covers any on-site power production system that interfaces with a utility supply and how they interconnect.
Find Us on Socials